An array of elegant cylindrical cutters, known as carbide ball burs, are crafted from various materials like tungsten carbide, diamond and steel to be employed for a variety of grinding, shaping and polishing tasks upon solid surfaces. Their dimensions span from 0.5mm to 1.6mm, endowing them with the flexibility to tackle any work at hand.
Carbide ball burs are frequently employed across a multitude of industries, from machining and manufacturing to jewelry and medical applications. These tools are quite useful for grinding, shaping, and polishing various materials like metals, jewels, and even bones.
Bolstered for operation with high-speed power tools, such as die grinders,rotary tools and dental drills, carbide ball burs are equipped to provide an impressive performance at a blistering speed of up to 200,000 rpm. However, the tremendous heat and pressure disparities that accompany this remarkable velocity cannot be ignored. It is therefore paramount that the materials with which these carbide ball burs are employed must have sufficiently robust characteristics to withstand such extreme conditions.
An array of sizes, designs, and shapes are available when it comes to carbide ball burs. The most commonly used sizes range from 0.5mm up to 1.6mm, each designed to construct a hole of its own dimensions and exfoliate a determined amount of material.
The project for which carbide ball bur is being employed can be identified by its shape. Typically, the most frequent shapes are round, cylindrical and cone-shaped designs. A round carbide ball bur is suited for basic grinding and sculpting purposes. On the other hand, cylindrical ball burs come in handy when creating holes and taking away material, while cone-shaped carbon ball burs are relevant for grinding and sculpting recessive surfaces.
Carbide ball burs can come equipped with many different cutting configurations. Single-cut burs contain a single row of cutting teeth, double-cut versions hold two rows, and multi-cut varieties present three or more lines of the teeth.
For toughness and durability, there’s no beating the incredible craftsmanship of tungsten carbide-based carbide ball burs. Renowned for their remarkable ability to withstand intense heat and pressure, these ball burs are manufactured from a range of materials including tungsten carbide, steel and even diamond. If you’re looking for a tool capable of enduring the toughest conditions, then these equipment must be your go-to!
Despite being not as durable as tungsten carbide, steel is employed as a beneficial material for producing ball burs due to its lower risk of breaking or shattering. Steel is a pliant metal that comes second only to tungsten carbide in terms of being chosen as the material for the composition of such tools.
Of all known materials, Diamond is the toughest, and also the most costly. For the challenging task of grinding and sculpting, Diamond carbide ball burs are employed.
For optimal performance, it is important to take care of your carbide ball burs in order to prolong their lifespan. These tools should be stored in a crisp, dry environment and lubricated with a light oil just prior to usage.
To make your carbide ball bur look like new, start off by brushing away any material stuck to its cutting teeth with a brush crafted for softness. Then, let it soak in a gentle detergent solution for half an hour. When you finish, rinse it thoroughly with clean water and use a gentle cloth to dry it.
If you need a bur that supports plenty of uses, then the 1.0-1.6mm carbide ball bur is the perfect choice. From grinding and shaping to removing and polishing, these dynamic burs can do it all.
Related Product
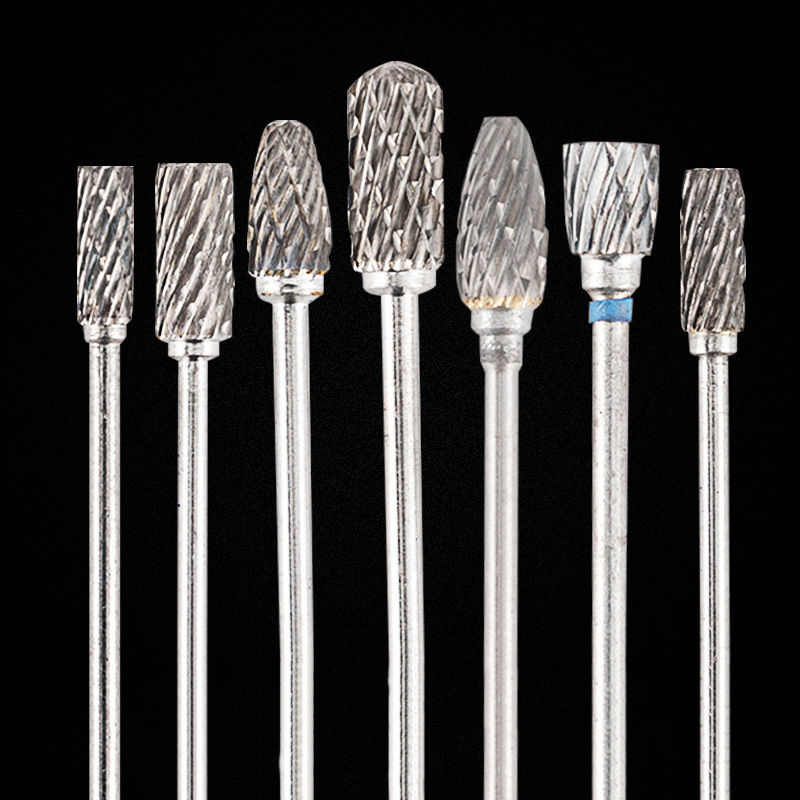
HP Deburring Carbide Burs
Product Information Brand MSK Material Tungsten Steel Model Grinding Head Custom Processing Yes Feature: The dental grinding head is made of tungsten steel with stabl […]
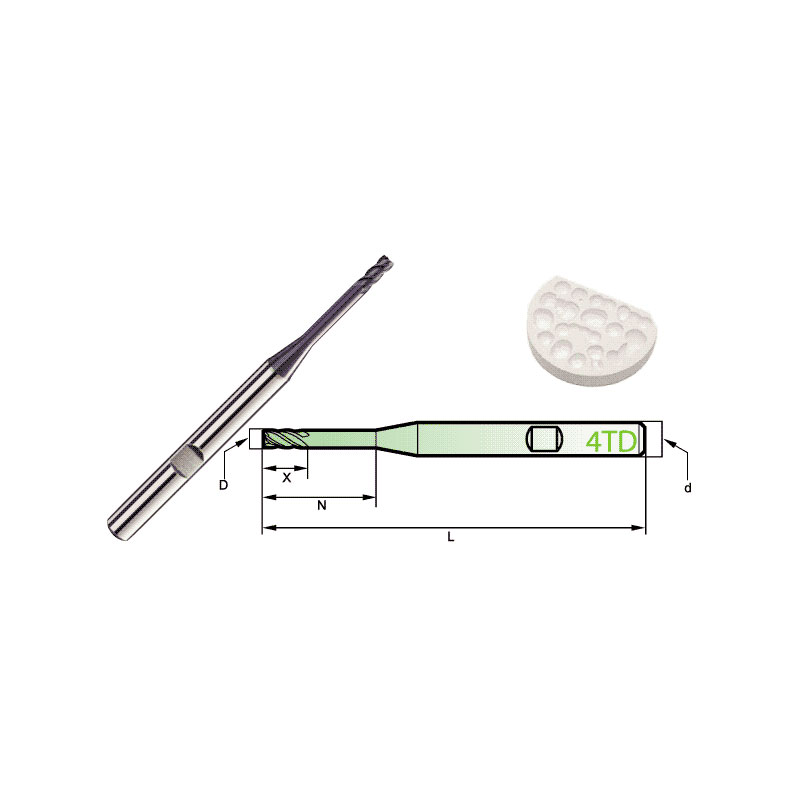
Carbide Roland CAD/CAM Burs
Product Information Origin Tianjing, China Brand MSK Number Of Blades 4 Product Name Dental Special 4-Blade End Mill Model D Number Of Blades Z X N L d 4TD2060HB 2 4 […]
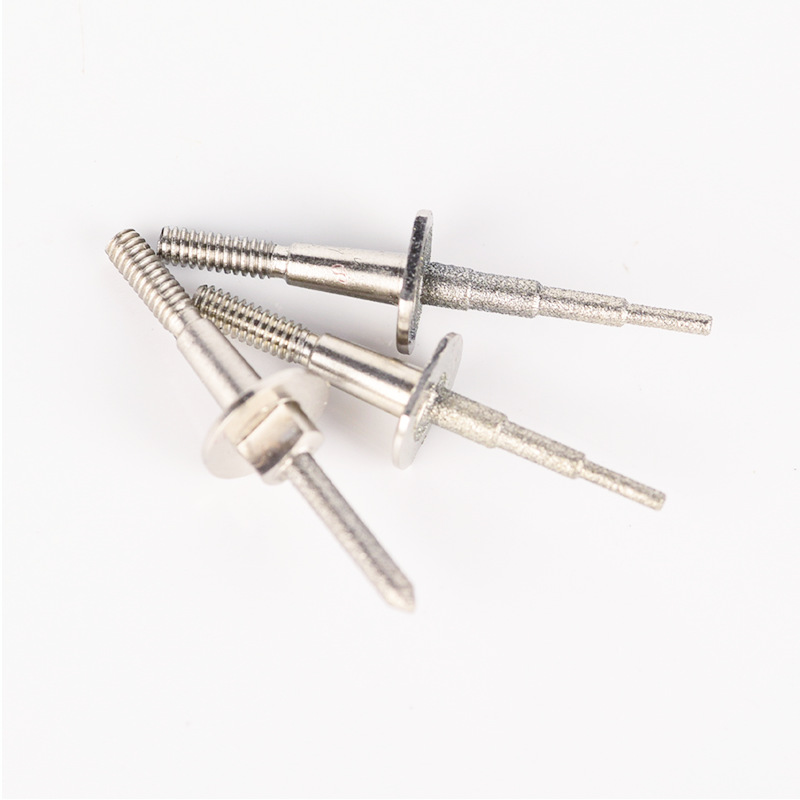
Step Bur Milling Bur Grinder for Glass Cerami
Product Information Origin Tianjing, China Shank Diameter 1.8 (mm) Brand MSK Scope Of Application CEREC3 Grinding Equipment Material Stainless Steel/Carbide Main Sales Areas […]
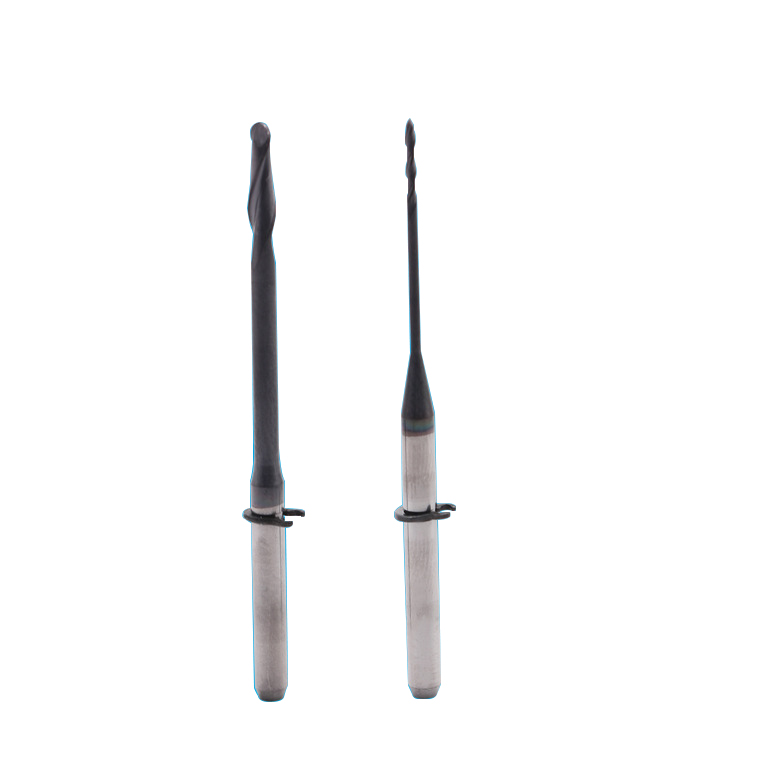
Dental CAD/CAM Milling Burs
Product Information Origin Tianjing, China Material Stainless Steel Brand MSK Applicable Machine Tools A Variety Of Options Custom Processing Yes Whether To Coat No Is It a […]
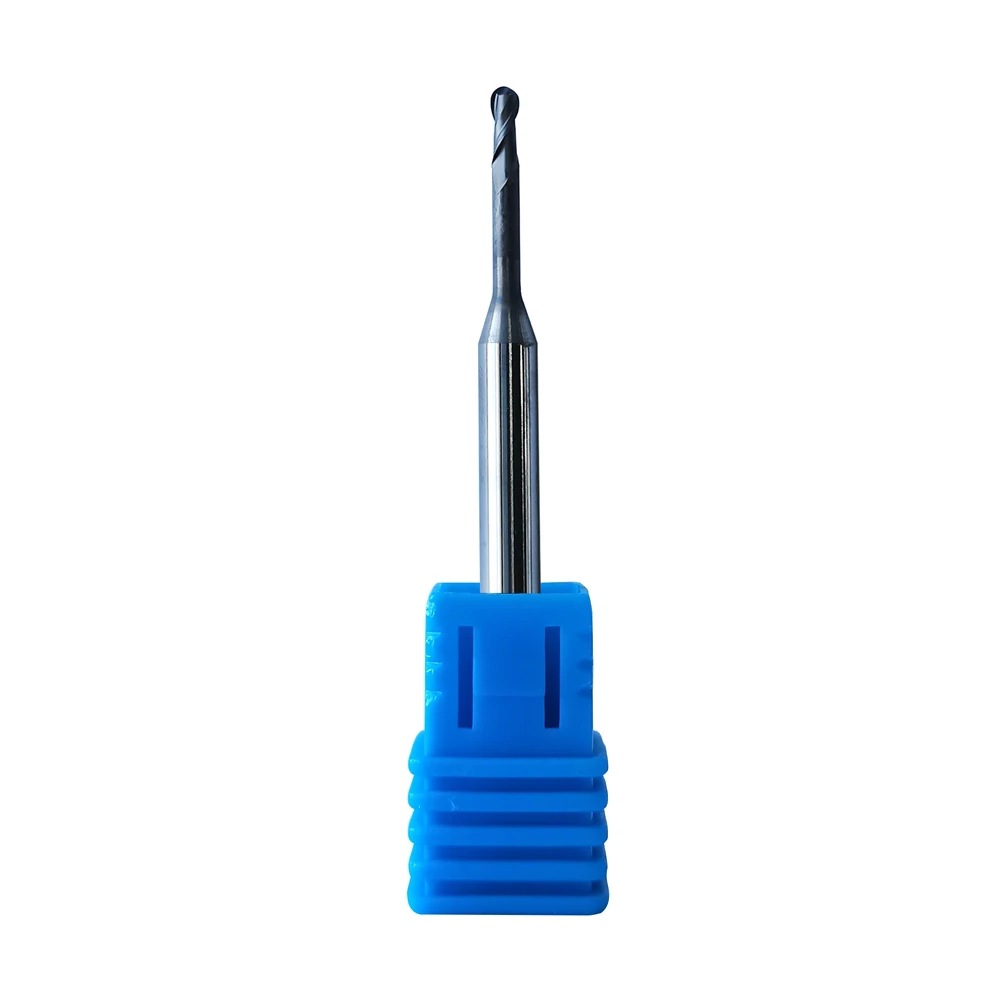
Supply Roland DLC Zirconia Burs
Product Information Origin Tianjing, China Series Dental Bur Brand MSK Cutting Edge Form 2 Blade/3 Blade Ball Diameter (Mm) 0.6, 1, 2 Material Very Fine Grained Cemented Car […]
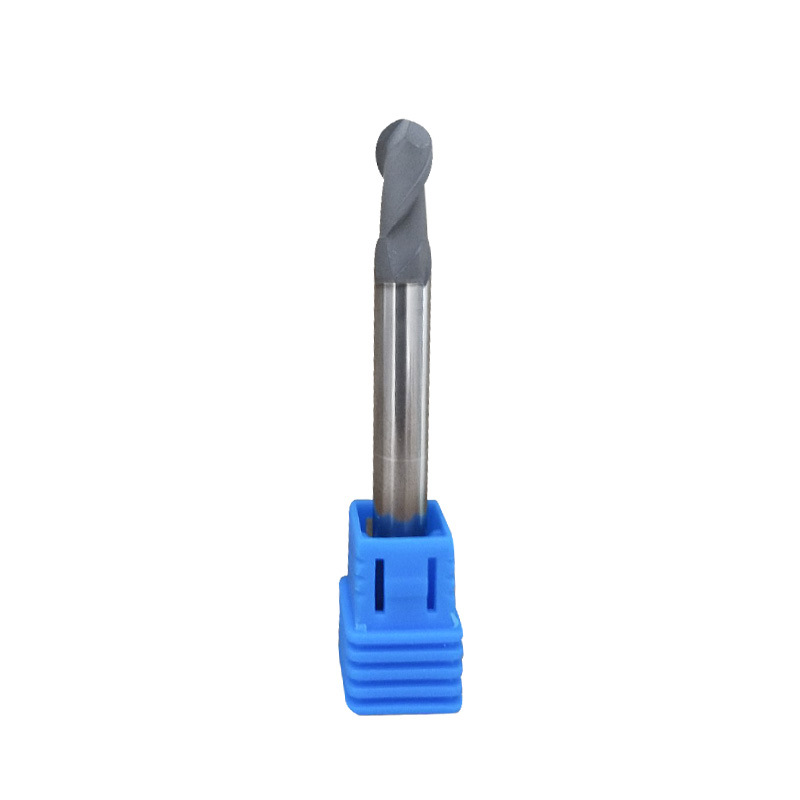
Diamond Coating Round Diamond Cutters
Product Information Origin Tianjing, China Series U Series Brand MSK Cutting Edge Form Helical Structure Ball Diameter (Mm) 3 Material Carbide Minimum Cutting Diameter At Th […]
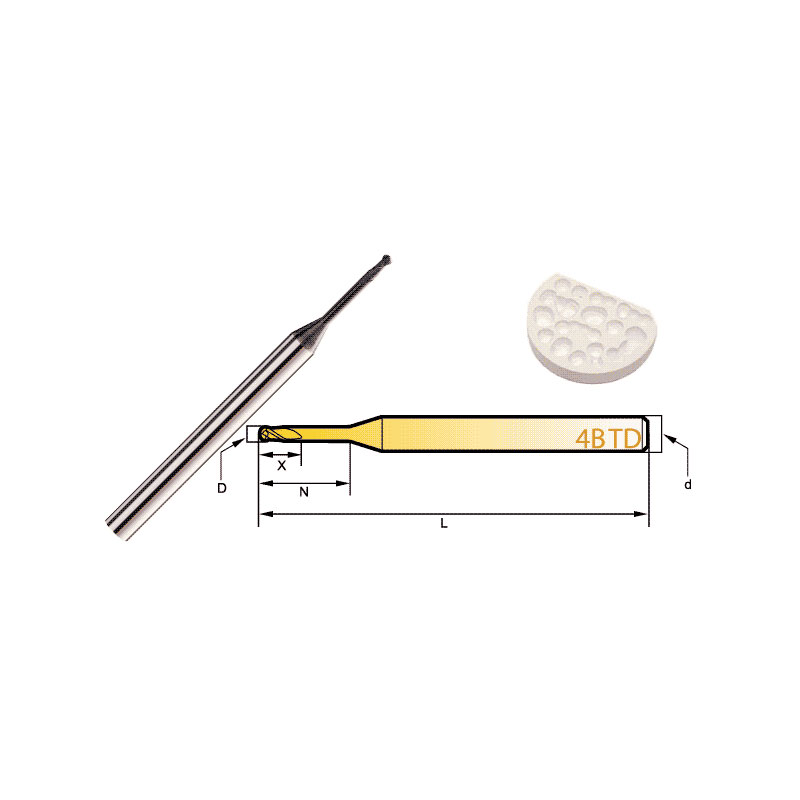
Diamond Bur Ball Round
Product Information Product Name Dental 4-Flute Ball End Mill Brand MSK Model D Number Of BladesZ X N L d 4BTD2060 2 4 6 6 50 3 4BTD2010 2 4 6 10 50 3 4BTD2016 2 4 6 […]
Post time: 2023-06-19