A carbide bur is a versatile, reliable tool used in industrial and construction processes. It can be found in a multitude of shapes and sizes, enabling a variety of functions, from the grinding and shaping of metal to drilling holes in concrete.
Drawing their durability and strength from a present-day staple, tungsten carbide, carbide burs can be composed of several diverse materials. Cobalt and titanium carbide are certainly reliable resources for specific applications, though tungsten carbide continues to dominate the field as the go-to choice for the majority of bur uses.
A wide selection of carbide bur options encompasses round, flat, and pointed varieties. Each shape is uniquely designed to execute different tasks; round burs usually act as grinding and sculpting tools when it comes to metal materials, whereas flat burs are more suited to activities such as hole-drilling.
It’s crucial to choose the perfect size and shape of carbide bur for the job at hand. From itsy-bitsy micro-burs to giant ones applicable for strenuous tasks – no task is too major or too minor for available sizes of carbide burs.
The bur size and shape are necessary considerations, but the material also matters. With three carbide bur choices, Tungsten, Cobalt, and Titanium, its paramount to select the one that best suits the needs of the job. All three have individual benefits and drawbacks, so do your research before you settle on the right one.
Exploring the Properties of Tungsten Carbide Burs
For projects that require prolonged resistance to wear and tear, tungsten carbide burs are the number one go-to choice. The superior durability of this material withstands high temperatures for extended periods of time. Choose from an array of sizes and shapes to properly fulfill your task – no matter the size or complexity.
Tungsten carbide is an incredibly tough material that has the ability to withstand serious levels of heat.
A broad assortment of forms and sizes exist in the collection of tungsten carbide burs.
Tungsten carbide burs are a versatile tool for numerous applications, from forming and refining metal objects to puncturing holes in concrete structures.
When compared to other carbide burs, tungsten carbide burs typically come with a bigger price tag.
-Handling tungsten carbide burs requires special caution; if misused, they can inflict considerable destruction.
Harnessing the Power of Cobalt Carbide Burs
A combination of cobalt and tungsten carbide creates cobalt carbide burs, which are becoming increasingly more popular because of their specific attributes. Although they are not as prevalent as tungsten carbide burs, their advantage in certain applications gives them an edge.
Cobalt carbide burs are a more economical choice than tungsten carbide burs.
Compared to tungsten carbide burs, cobalt carbide burs provide better control when used.
Unlike tungsten carbide burs, cobalt carbide burs are far less likely to incur damage.
Cobalt carbide burs are not as long lasting when compared to their tungsten carbide counterparts.
Cobalt carbide burs, unlike their tungsten-carbide counterparts, don’t come in a wide array of shapes and sizes.
Unleashing the Marvels of Titanium Carbide Burs
Combining titanium and tungsten carbide, titanium carbide burs are a rather rare variant of its carbide counterpart. Still, this distinctive type of bur is on the rise in terms of popularity due to the special characteristics it has to offer.
Titanium carbide burs prove to be sturdier and longer-lasting than their tungsten carbide counterparts.
With superior durability, titanium carbide burs provide greater protection against the wear and tear that can result from use compared to tungsten carbide burs.
An array of shapes and sizes are present in the collection of titanium carbide burs.
When it comes to carbide burs, titanium ones come at a higher price than their tungsten counterparts.
-Proficiency with titanium carbide burs is essential as they can be detrimental if manipulated without due care.
Related Product
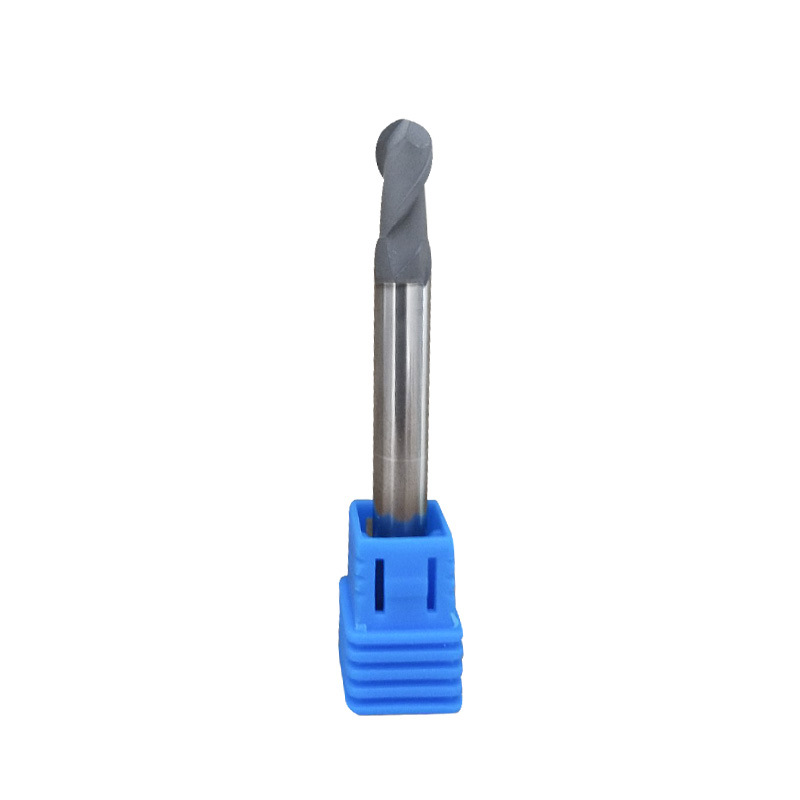
Diamond Coating Round Diamond Cutters
Product Information Origin Tianjing, China Series U Series Brand MSK Cutting Edge Form Helical Structure Ball Diameter (Mm) 3 Material Carbide Minimum Cutting Diameter At Th […]
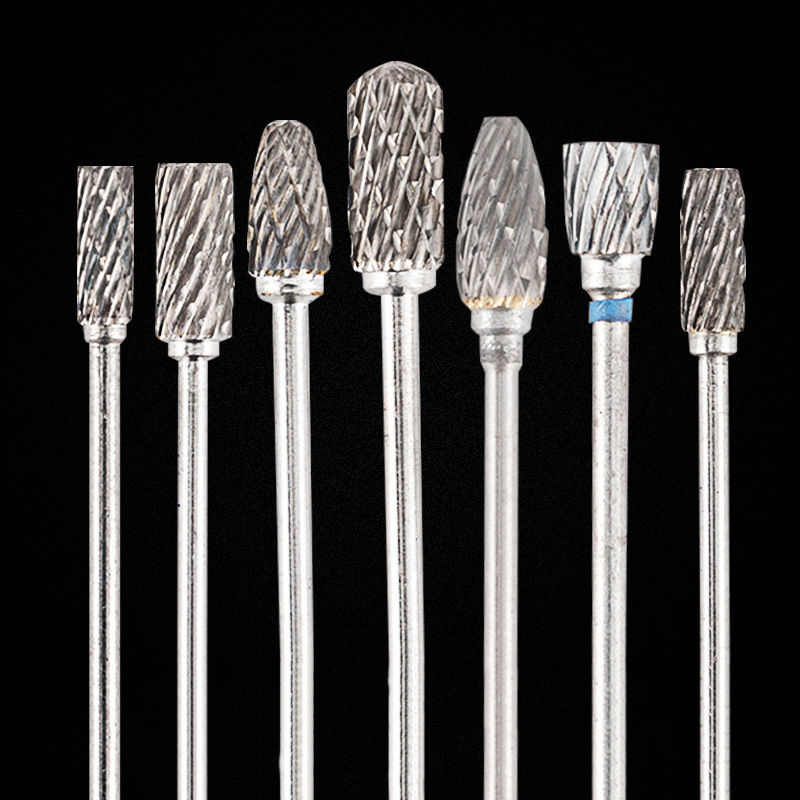
HP Deburring Carbide Burs
Product Information Brand MSK Material Tungsten Steel Model Grinding Head Custom Processing Yes Feature: The dental grinding head is made of tungsten steel with stabl […]
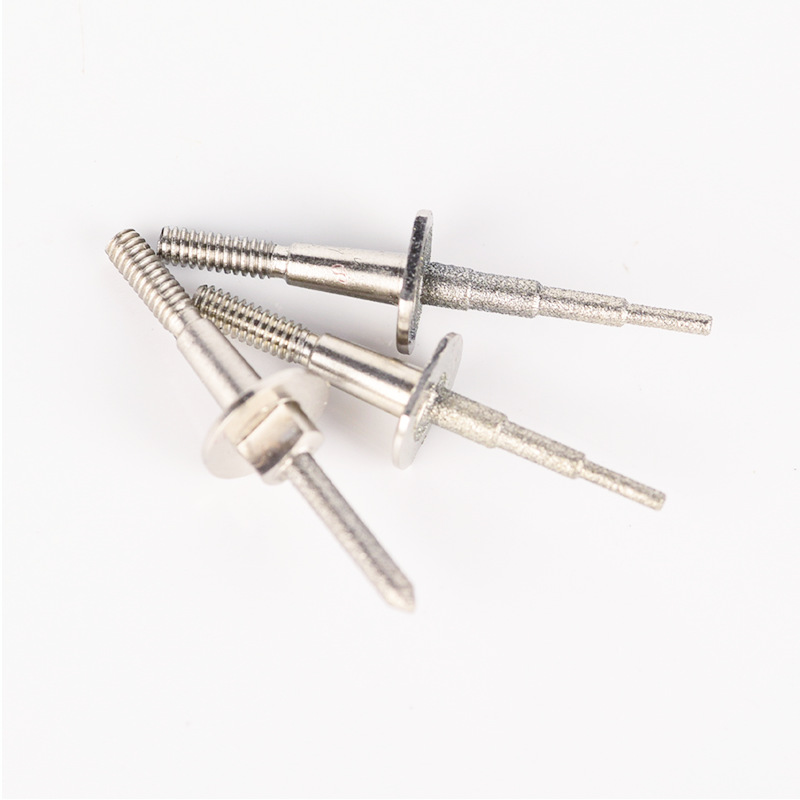
Step Bur Milling Bur Grinder for Glass Cerami
Product Information Origin Tianjing, China Shank Diameter 1.8 (mm) Brand MSK Scope Of Application CEREC3 Grinding Equipment Material Stainless Steel/Carbide Main Sales Areas […]
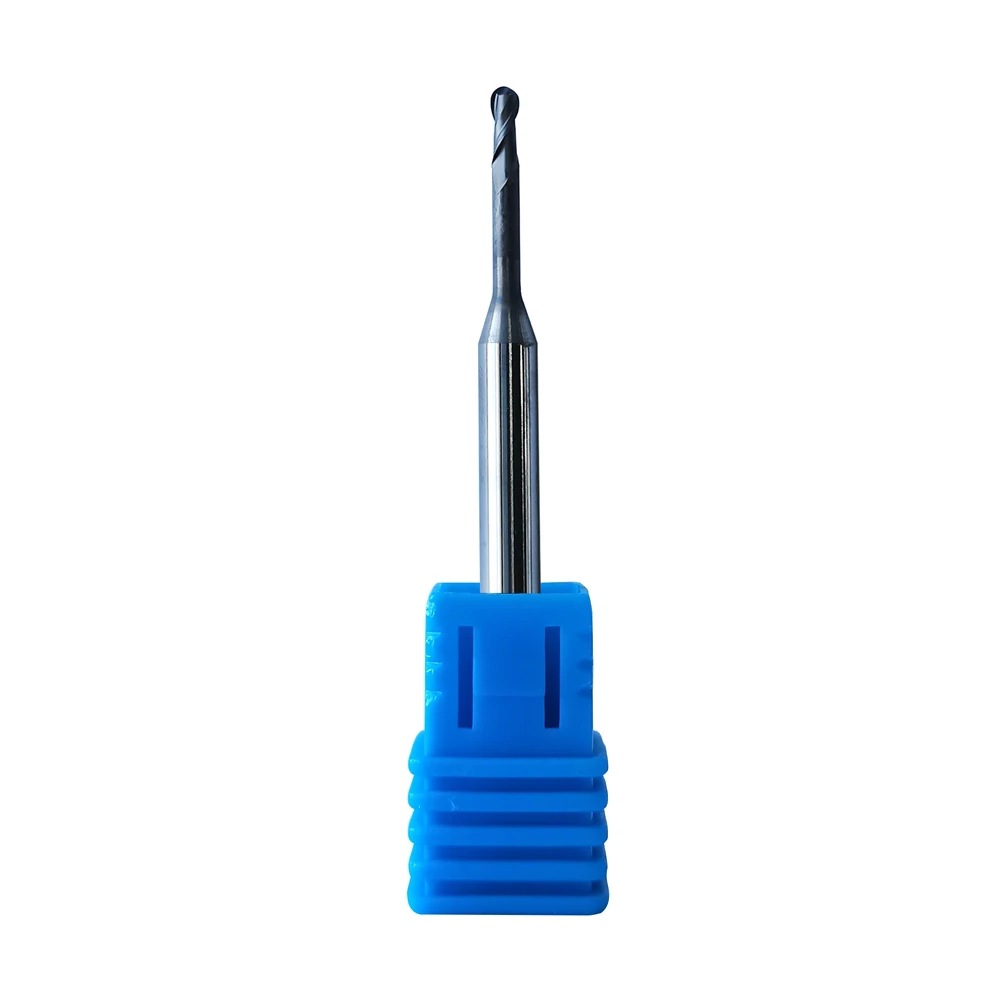
Supply Roland DLC Zirconia Burs
Product Information Origin Tianjing, China Series Dental Bur Brand MSK Cutting Edge Form 2 Blade/3 Blade Ball Diameter (Mm) 0.6, 1, 2 Material Very Fine Grained Cemented Car […]
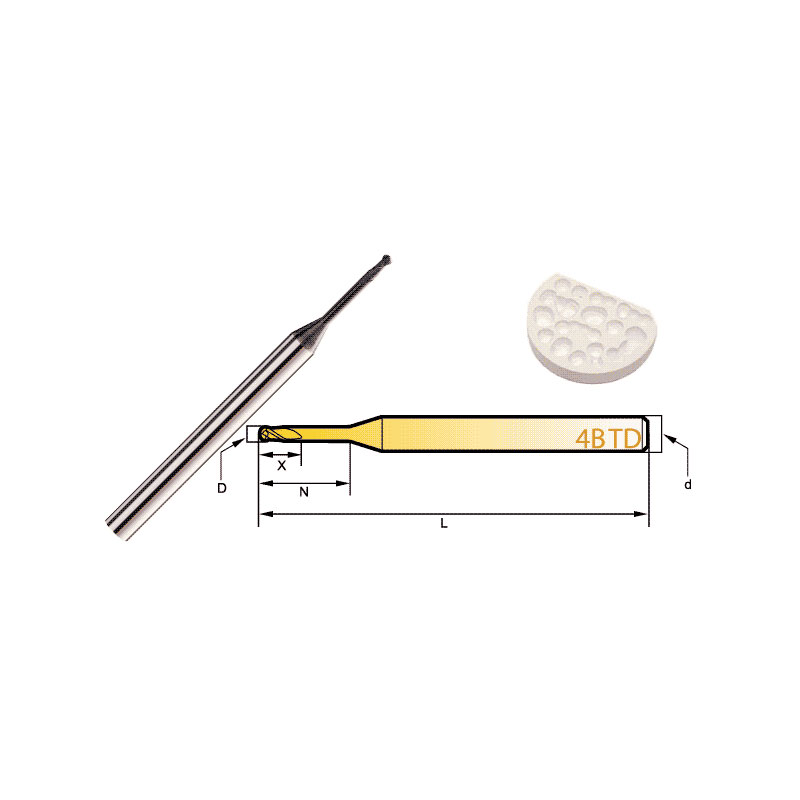
Diamond Bur Ball Round
Product Information Product Name Dental 4-Flute Ball End Mill Brand MSK Model D Number Of BladesZ X N L d 4BTD2060 2 4 6 6 50 3 4BTD2010 2 4 6 10 50 3 4BTD2016 2 4 6 […]
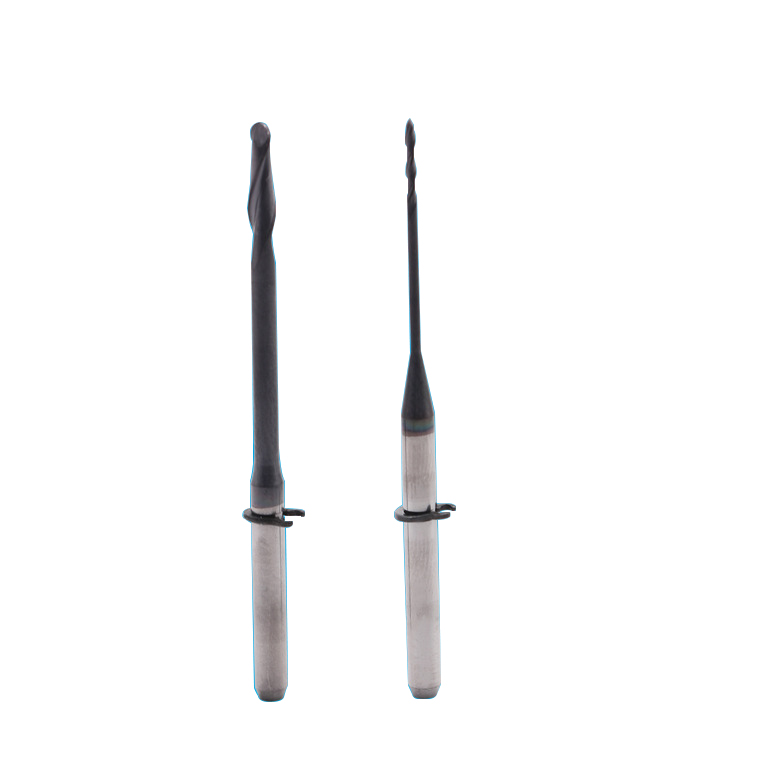
Dental CAD/CAM Milling Burs
Product Information Origin Tianjing, China Material Stainless Steel Brand MSK Applicable Machine Tools A Variety Of Options Custom Processing Yes Whether To Coat No Is It a […]
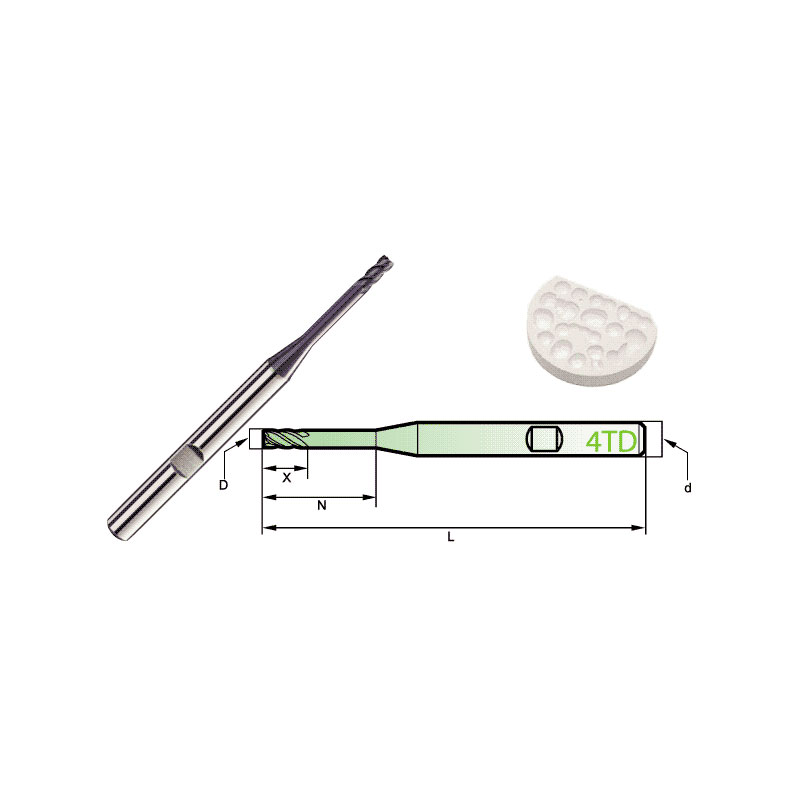
Carbide Roland CAD/CAM Burs
Product Information Origin Tianjing, China Brand MSK Number Of Blades 4 Product Name Dental Special 4-Blade End Mill Model D Number Of Blades Z X N L d 4TD2060HB 2 4 […]
Post time: 2023-06-25