To cut, shape, and remove materials from a workpiece, a carbide bur is essential. Crafted from various materials such as steel, other metals, and the strongest of them all – carbide – this specialized tool has a cutting edge far sharper than that of its steel counterpart.
A range of sizes and shapes of carbide burs are accessible, enabling them to be used for machining, drilling, grinding, as well as medical and dental operations. Their breadth of applications make them an excellent tool for professionals in many different fields.
Cylindrical carbide burs are one of the more widely employed varieties, and can be utilized for a plethora of operations. They come in a range of sizes, from those expedient for creating tiny holes in metal, to their larger counterparts used for their effectiveness on vast surfaces. In general, these burs are excellent for tasks like drilling, boring, and reaming.
When tackling various grinding and finishing operations, ball-shaped carbide burs prove to be an excellent tool. As they come in numerous sizes, from miniscule to amounting those ideal for larger projects, they offer versatility and reliability during any job. Whether you’re working on a petite surface or a larger one, these burs will ensure that the job is a successful one.
A diverse range of carbide burs are up for grabs, such as oval, triangular, and rectangular. Each type is specially designed to fit different tasks – oval carbide burs are in high demand for smoothing operations, while triangle carbide burs are suitable for drilling purposes.
A variety of materials, from tungsten carbide and cobalt to steel, compose the construction of a carbide bur. With the choice of material impacting both its price and strength, one must take great care in selecting the right bur for their needs.
When it comes to crafting carbide burs, tungsten carbide is king. Known for its unrivaled durability and resistance to abrasion, tungsten carbide burs may come with a heftier price tag than cobalt or steel variants, but the investment is always worth the extra cost.
Unlike the hardiness of tungsten carbide burs, cobalt burs are less costly yet are not as resistant to wear. Nonetheless, they make a viable option when manufacturing carbide burs since their composition is still largely cobalt in nature.
Steel burs offer the lowest cost among the types of carbide burs, but are less wear-resistant than their counterparts made of tungsten carbide and cobalt. Despite not being as tough as other carbides, steel still remains a very hard material.
Related Product
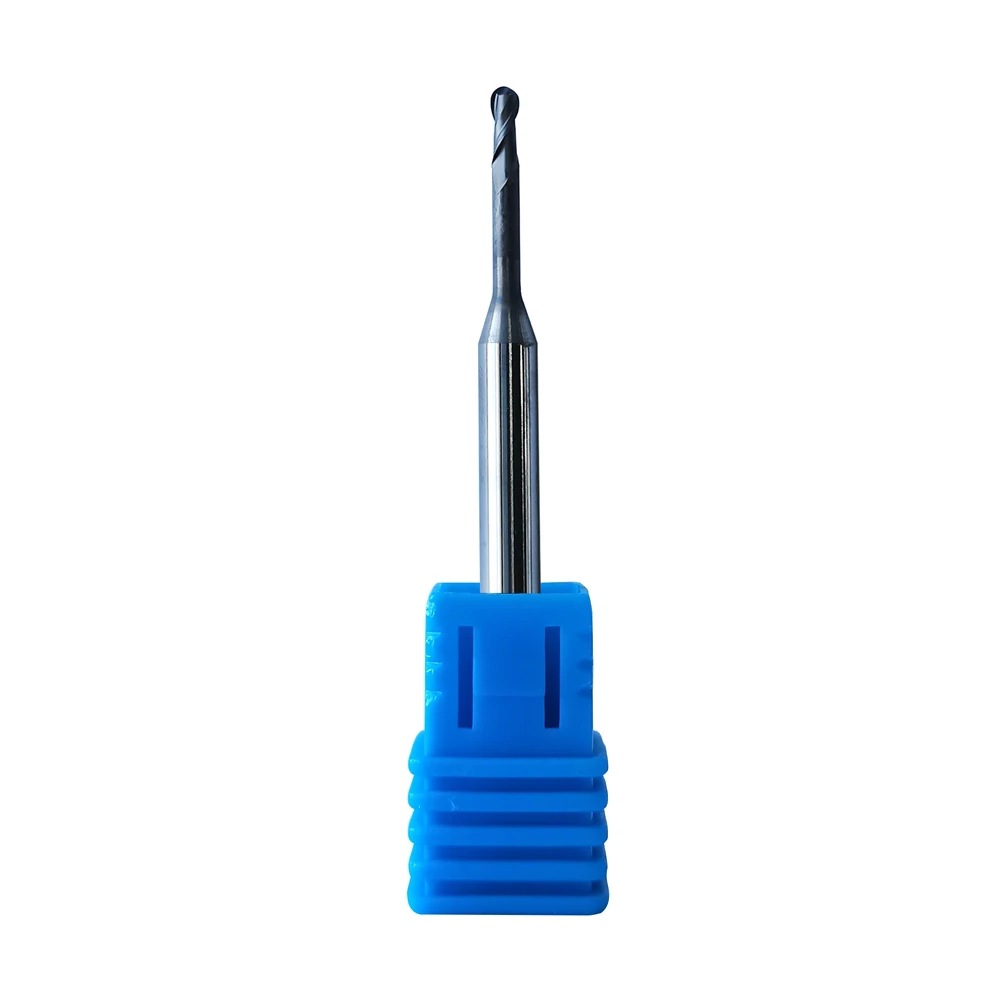
Supply Roland DLC Zirconia Burs
Product Information Origin Tianjing, China Series Dental Bur Brand MSK Cutting Edge Form 2 Blade/3 Blade Ball Diameter (Mm) 0.6, 1, 2 Material Very Fine Grained Cemented Car […]
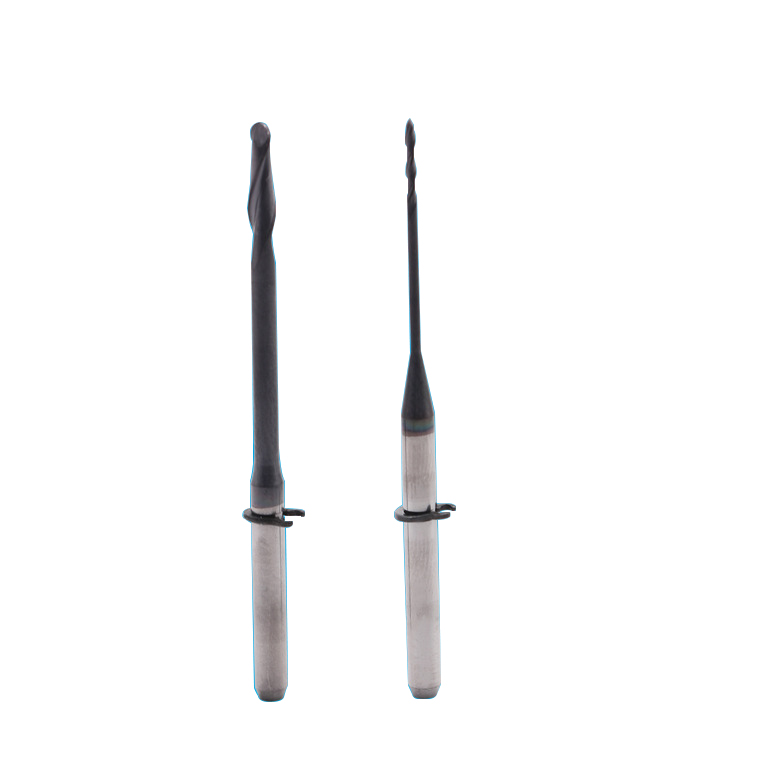
Dental CAD/CAM Milling Burs
Product Information Origin Tianjing, China Material Stainless Steel Brand MSK Applicable Machine Tools A Variety Of Options Custom Processing Yes Whether To Coat No Is It a […]
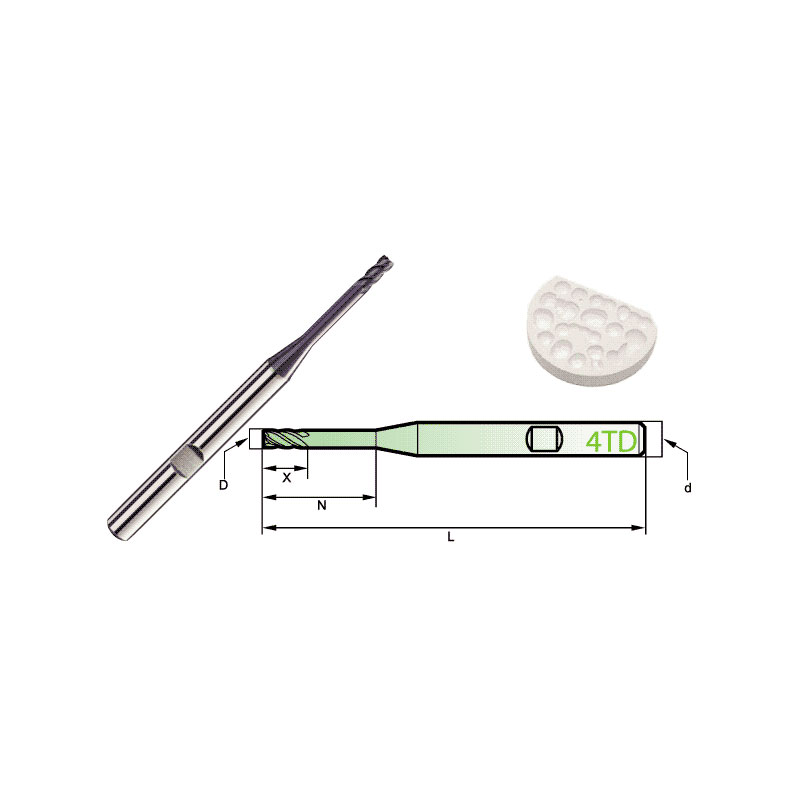
Carbide Roland CAD/CAM Burs
Product Information Origin Tianjing, China Brand MSK Number Of Blades 4 Product Name Dental Special 4-Blade End Mill Model D Number Of Blades Z X N L d 4TD2060HB 2 4 […]
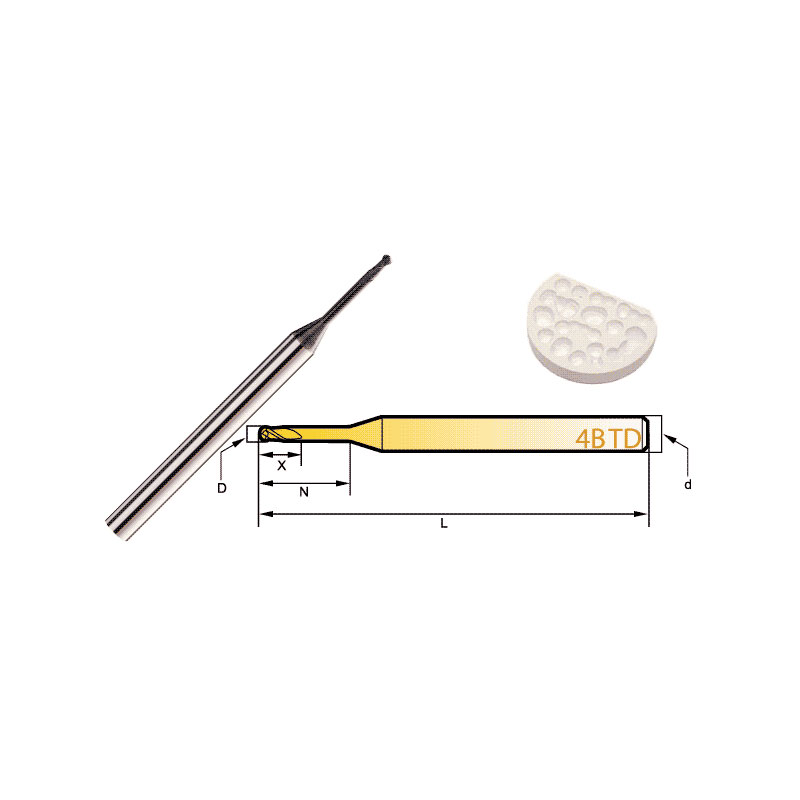
Diamond Bur Ball Round
Product Information Product Name Dental 4-Flute Ball End Mill Brand MSK Model D Number Of BladesZ X N L d 4BTD2060 2 4 6 6 50 3 4BTD2010 2 4 6 10 50 3 4BTD2016 2 4 6 […]
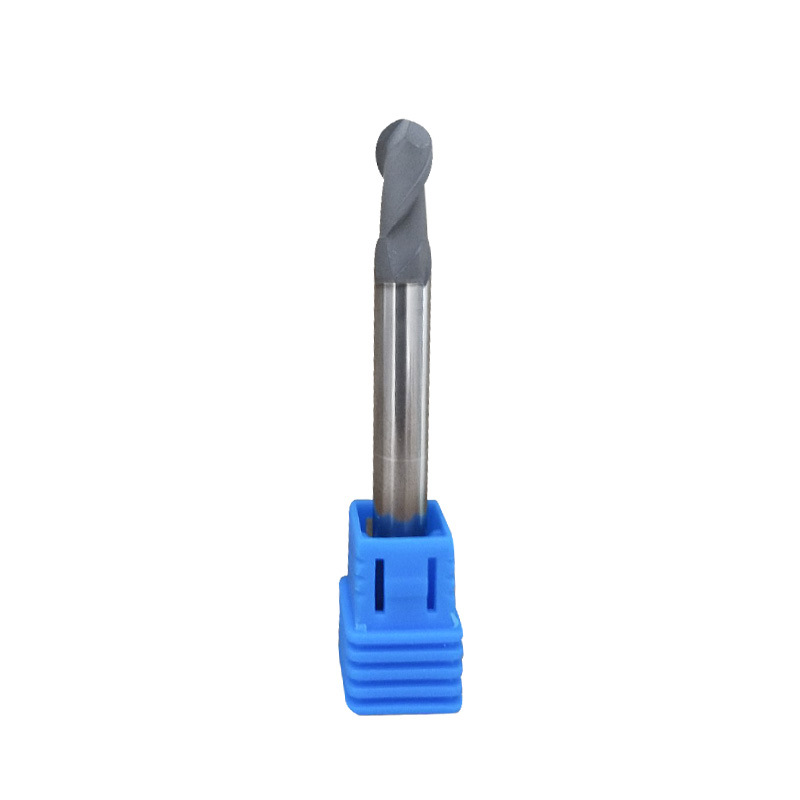
Diamond Coating Round Diamond Cutters
Product Information Origin Tianjing, China Series U Series Brand MSK Cutting Edge Form Helical Structure Ball Diameter (Mm) 3 Material Carbide Minimum Cutting Diameter At Th […]
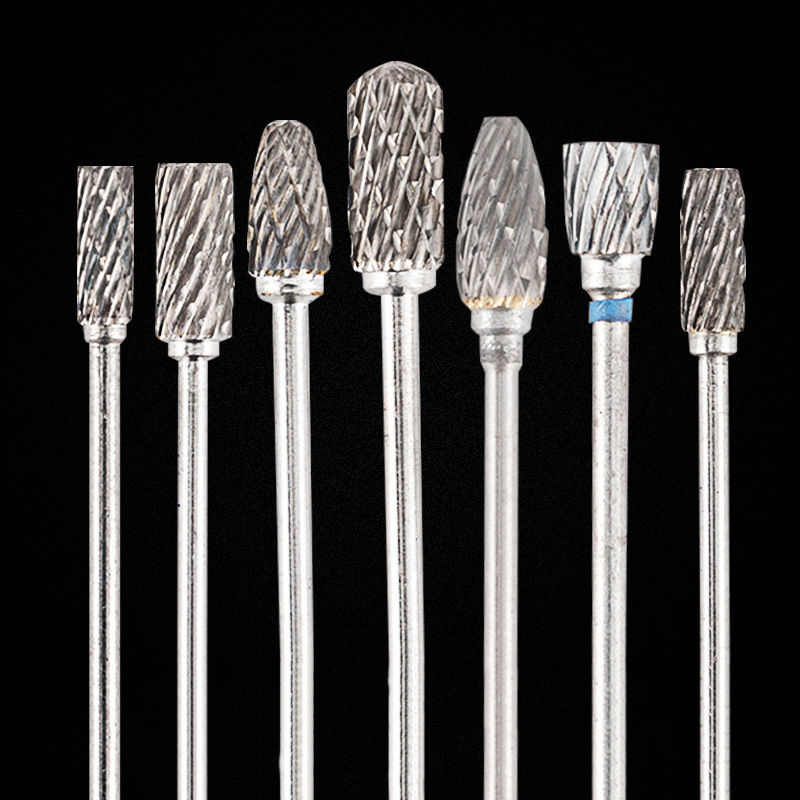
HP Deburring Carbide Burs
Product Information Brand MSK Material Tungsten Steel Model Grinding Head Custom Processing Yes Feature: The dental grinding head is made of tungsten steel with stabl […]
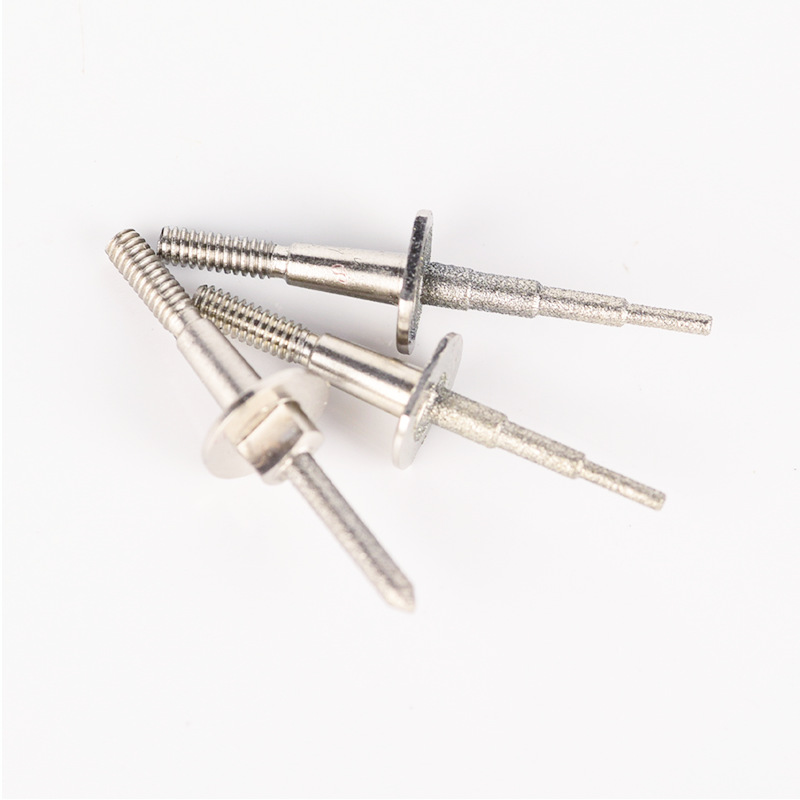
Step Bur Milling Bur Grinder for Glass Cerami
Product Information Origin Tianjing, China Shank Diameter 1.8 (mm) Brand MSK Scope Of Application CEREC3 Grinding Equipment Material Stainless Steel/Carbide Main Sales Areas […]
Post time: 2023-07-01