Tungsten carbide burs are the go-to cutting tools of choice for a multitude of grinding, shaping, and material removal projects. They come in a range of distinctive shapes, sizes, and styles which makes them highly effective and versatile for a variety of purposes.
From minor detailing to wide coverings, cylindrical shaped carbide burs meet the demands of many materials, such as metals, ceramics, plastics and glass. A myriad of sizes can be found, from small to grandiose, allowing a variety of projects to be tackled with ease. For intricate shaping, the smaller burs are best suited; while for more expansive segments, the larger options will do the job swiftly and appropriately.
An array of carbide-constructed burs can be harnessed to cut through a plethora of surfaces. In terms of shape, they come in many forms, including:
Utilized in applications such as metalworking, plastic shaping, and timber cutting, cutting burs easily chisel away at material, sculpting the surface as desired.
Despite their hard-as-rock composition, carbide burs are not impervious to destruction. Using them on unbearably hard materials or clumsily dropping them can easily bring an end to their vast capabilities.
The successful use of carbide burs requires precision when it comes to speed and pressure. Go too hard and you may fracture your trusty bur. Too soft and it won’t manage to make the necessary cut.
From drill presses to die grinders, incorporating carbide burs into your power tool repertoire can prove advantageous for a wide array of projects.
An array of shank sizes is offered for those seeking carbide burs, such as:
An ubiquitous fixture in grinding and shaping operations, cylindrical shaped carbide burs can be employed on a variety of materials such as glass, ceramics, plastics and metals. Spanning an impressively varied size range, from diminutive to vast, these burs are ideal for both detailed and widespread applications.
For cutting different materials, carbide burs come in a host of shapes, including:
Utilitarian in nature, cutting burs are widely employed in the fabrication of a wide array of materials such as metal, wood, and plastic, as well as for the removal of particles from a surface.
Despite their extraordinary toughness, carbide burs are not impervious to breakage. They may be compromised if utilized on extremely tough materials or if subjected to a hard fall.
To obtain optimum performance from carbide burs, it is essential to understand the correct speed and pressure to apply. Applying too much force or employing a speed which is too high can be disastrous, potentially causing the bur to shatter. On the other hand, a poor result could be realized if the bur is used at a rate which is too slow.
A range of power tools can be complemented by the application of carbide burs, such as:
Bur users will find a wide range of shank sizes available when selecting carbide burs, including:
Related Product
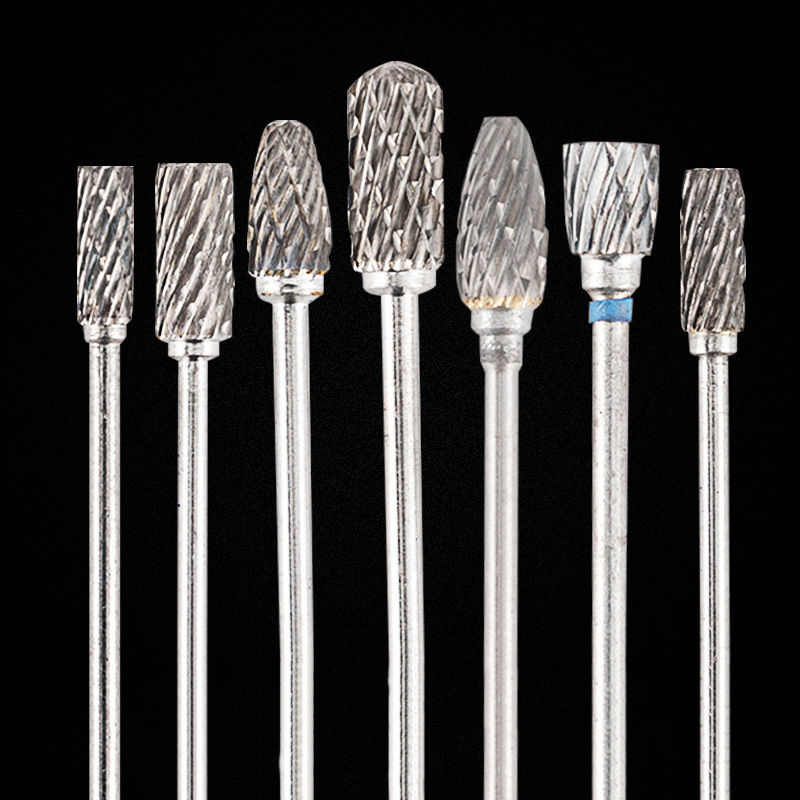
HP Deburring Carbide Burs
Product Information Brand MSK Material Tungsten Steel Model Grinding Head Custom Processing Yes Feature: The dental grinding head is made of tungsten steel with stabl […]
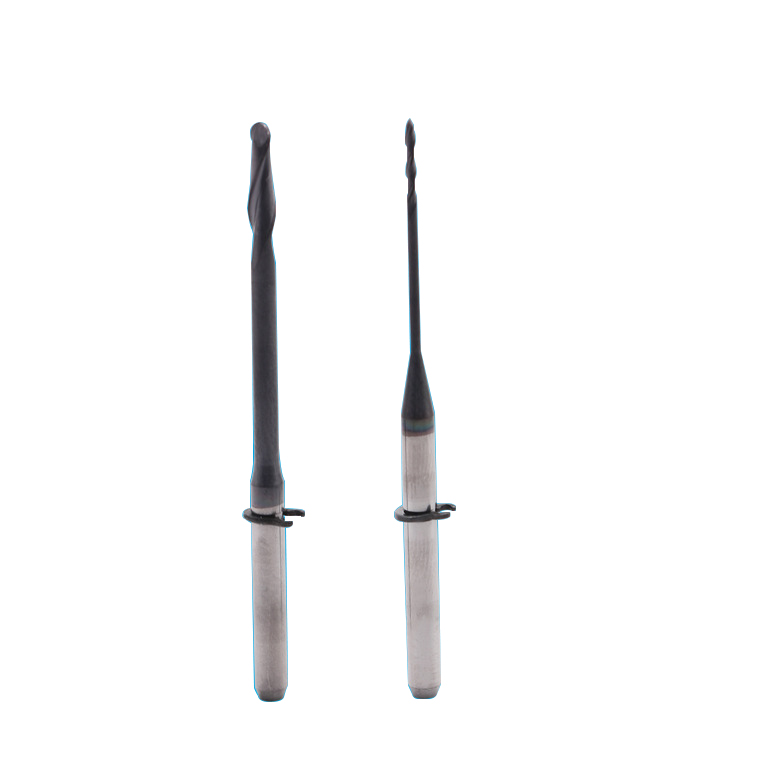
Dental CAD/CAM Milling Burs
Product Information Origin Tianjing, China Material Stainless Steel Brand MSK Applicable Machine Tools A Variety Of Options Custom Processing Yes Whether To Coat No Is It a […]
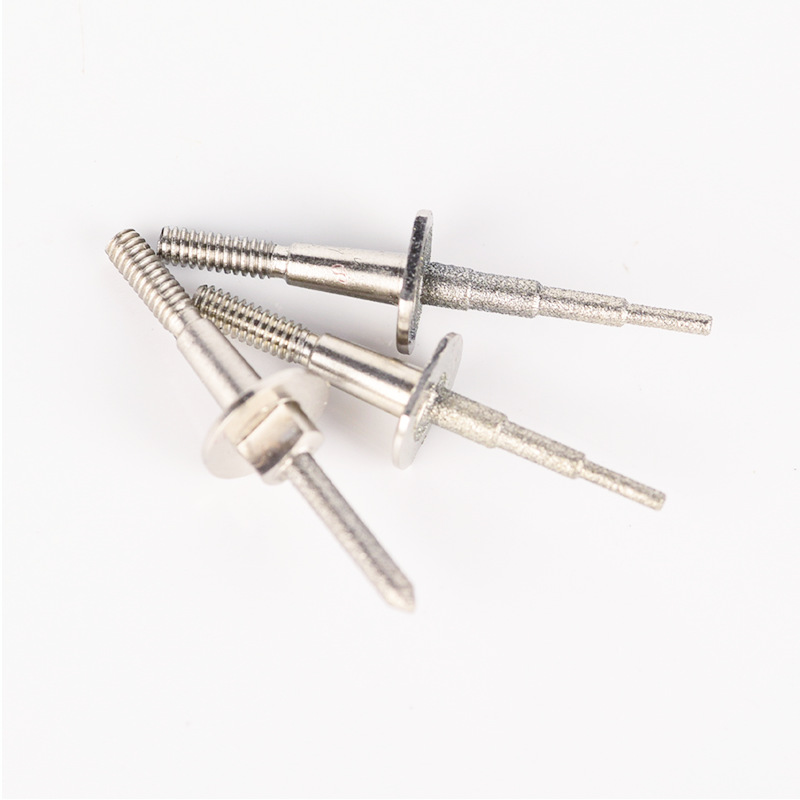
Step Bur Milling Bur Grinder for Glass Cerami
Product Information Origin Tianjing, China Shank Diameter 1.8 (mm) Brand MSK Scope Of Application CEREC3 Grinding Equipment Material Stainless Steel/Carbide Main Sales Areas […]
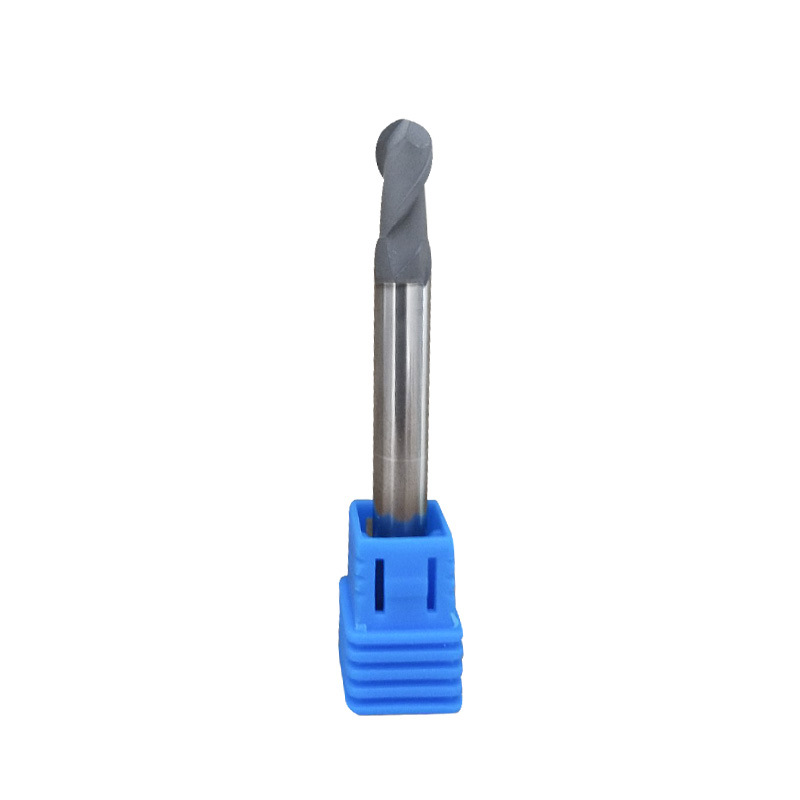
Diamond Coating Round Diamond Cutters
Product Information Origin Tianjing, China Series U Series Brand MSK Cutting Edge Form Helical Structure Ball Diameter (Mm) 3 Material Carbide Minimum Cutting Diameter At Th […]
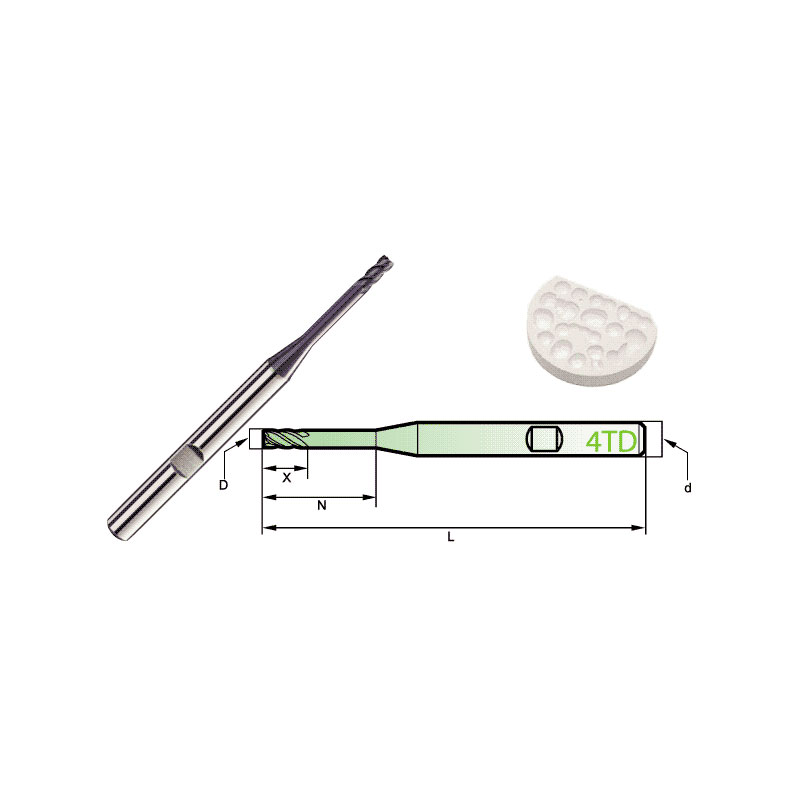
Carbide Roland CAD/CAM Burs
Product Information Origin Tianjing, China Brand MSK Number Of Blades 4 Product Name Dental Special 4-Blade End Mill Model D Number Of Blades Z X N L d 4TD2060HB 2 4 […]
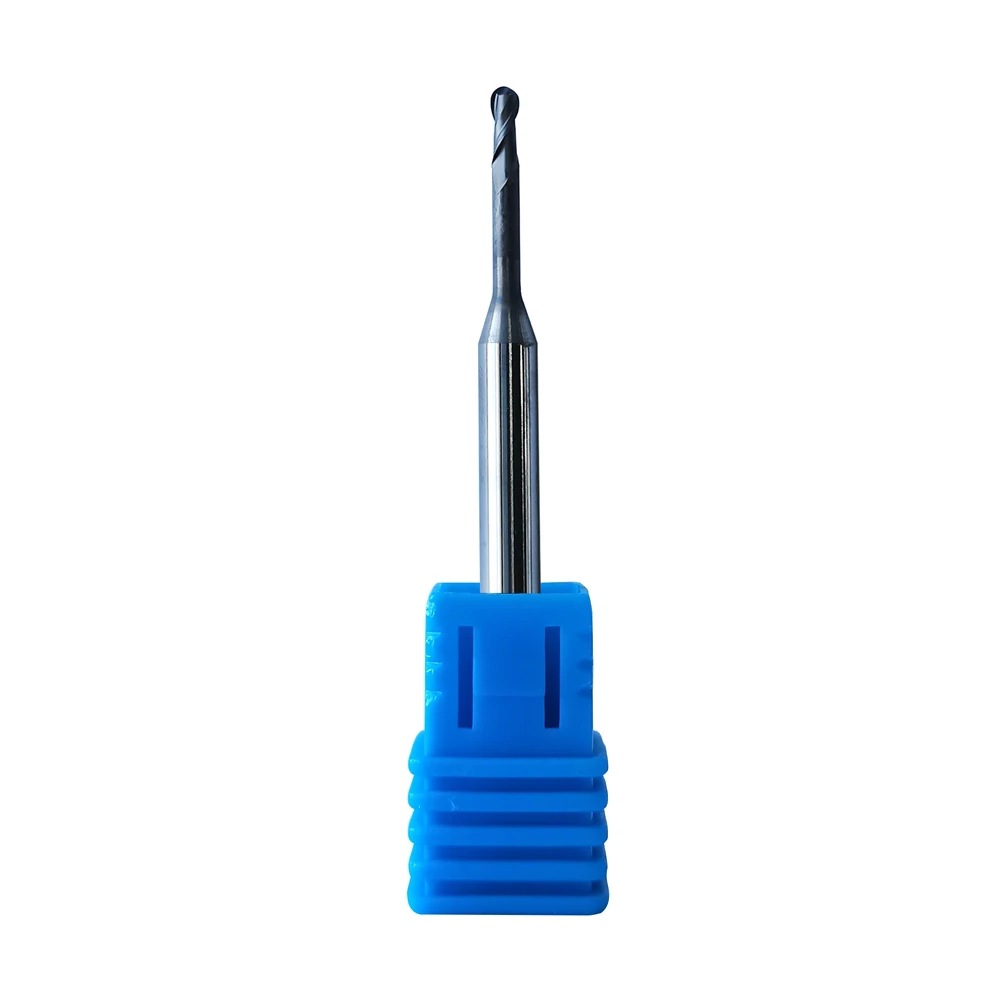
Supply Roland DLC Zirconia Burs
Product Information Origin Tianjing, China Series Dental Bur Brand MSK Cutting Edge Form 2 Blade/3 Blade Ball Diameter (Mm) 0.6, 1, 2 Material Very Fine Grained Cemented Car […]
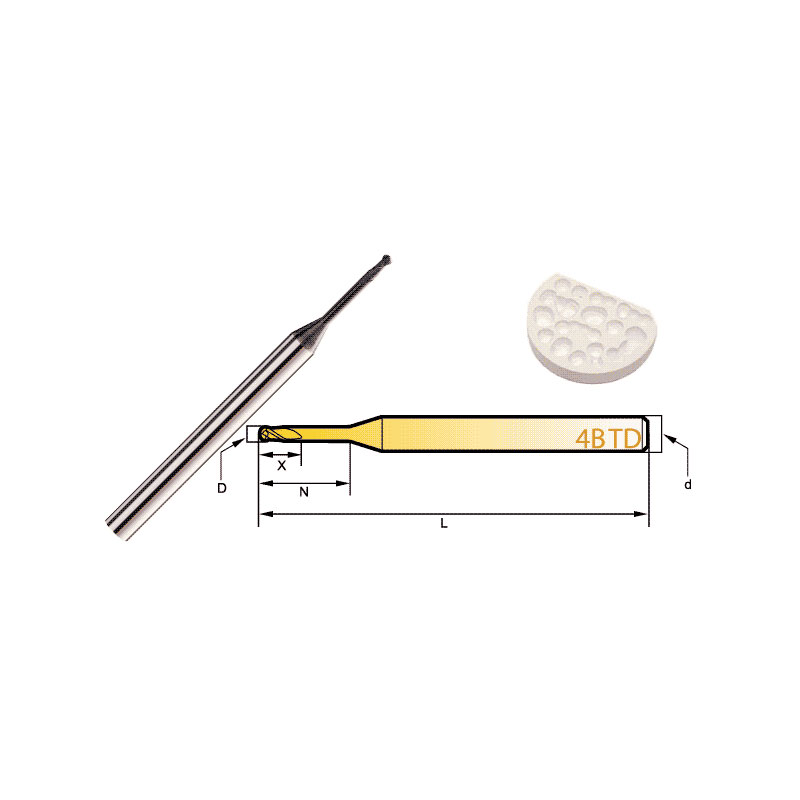
Diamond Bur Ball Round
Product Information Product Name Dental 4-Flute Ball End Mill Brand MSK Model D Number Of BladesZ X N L d 4BTD2060 2 4 6 6 50 3 4BTD2010 2 4 6 10 50 3 4BTD2016 2 4 6 […]
Post time: 2023-06-25