A rotary cutting tool, the carbide bur is suitable for use in a die grinder. Its tungsten-carbide composition lends it remarkable strength and sturdiness. Moreover, these tools come in a vast array of sizes and shapes, making them a versatile choice for numerous projects.
Handheld and powerful, die grinders are used to smoothly shape the surfaces of multiple materials. Through its rotating carbide bur, this tool can be utilized to grind, sand, or polish in autobody shops, metal fabrication workshops, and woodcarving studios alike. Whether you need to shave off sharp edges or refine a smooth surface, die grinders are the perfect tool for the job.
Working at lightning-quick speeds, the operator manipulates a die grinder to carve away at the workpiece with a specialized carbide bur. This versatile tool can not only facilitate material removal but also craft refined, polished surfaces.
Working with different materials may require burs of varying shapes and sizes. Those made out of carbide are the most popular, with three shapes typically available – cylindrical, ball, and flame. Depending on the project, small or large carbide burs can be chosen to facilitate precise or heavier material removal.
A sphere of carbide, commonly referred to as a carbide bur, is a multi-functional tool that can be employed for a multitude of projects, including sculpting, cleaning edges, and polishing. Its round shape makes it accessible in various sizes, ranging from petite to sizable.
For more precision, cylindrical carbide burs are the ideal tool for grinding and finishing operations. Available in different sizes, from tiny to substantial, these burs will give you the results you need.
Aggressive material removal is made easier by the use of flame shaped carbide burs. There is a broad range of sizes available, from miniature to colossal.
When choosing a carbide bur, the grade of material should be considered. Soft grade burrs are suitable for tasks that require a gentle touch, while hard grade burrs are ideal for tougher jobs that call for an extra level of abrasion. Depending on the material being worked on, you can choose from a variety of grades, namely soft, medium, or hard.
With the selection between coated or non-coated, carbide burs come in various defenses against wear and tear. These protective coatings extend the lifetime of these tools, granting them greater durability than burs that lack such layers. Thus, investing in a version covered in armor will pay dividends by contributing to a longer lifespan for your bur.
A commonly applied surface treatment for carbide burs is the wear-resistant and resilient titanium nitride (TiN). This surface layer manifests in a variety of colors, such as black, gold, and silver, to suit a range of preferences.
For applications where extended endurance is a necessity, diamond-coated carbide burs are the optimal choice. Although more expensive than standard carbide burs, their robust quality will improve longevity and thereby save money in the long run. What’s more, they come in a variety of hues – from the striking black, blue, and green varieties – to further add to their overall appeal.
A range of prices can be found for carbide burs, based off the size, shape, strength-grade, and what type of finish they have. Many brand-name providers like Dremel, Foredom, and Milwaukee offer the burs in their catalogs.
When deciding upon a carbide bur for a task, three aspects must be taken into account: size, shape, and grade. It is also imperative to account for the coating on the bur that could make all the difference to complete the job safely and effectively.
Related Product
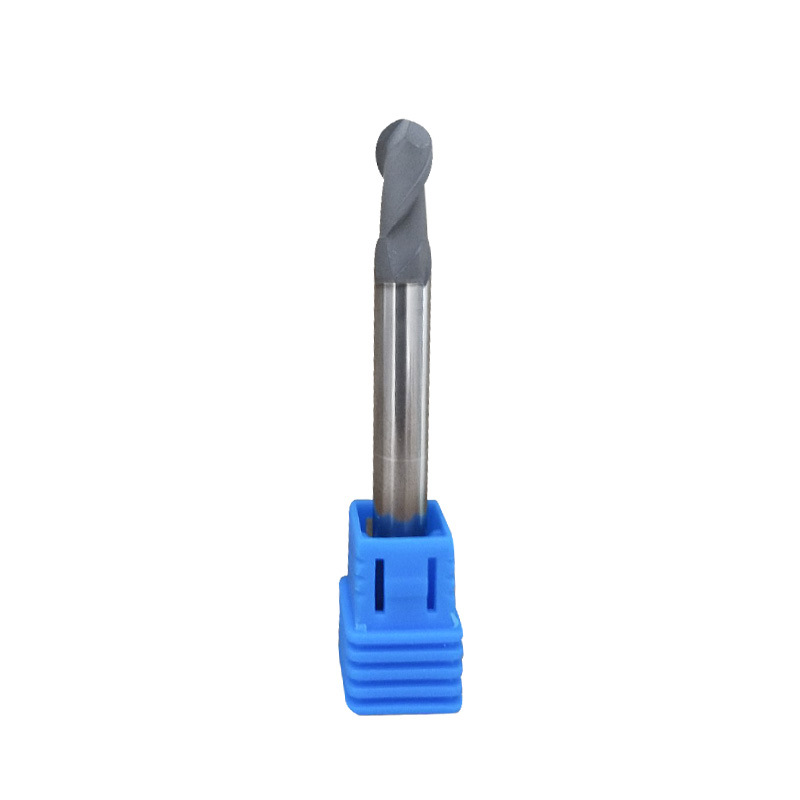
Diamond Coating Round Diamond Cutters
Product Information Origin Tianjing, China Series U Series Brand MSK Cutting Edge Form Helical Structure Ball Diameter (Mm) 3 Material Carbide Minimum Cutting Diameter At Th […]
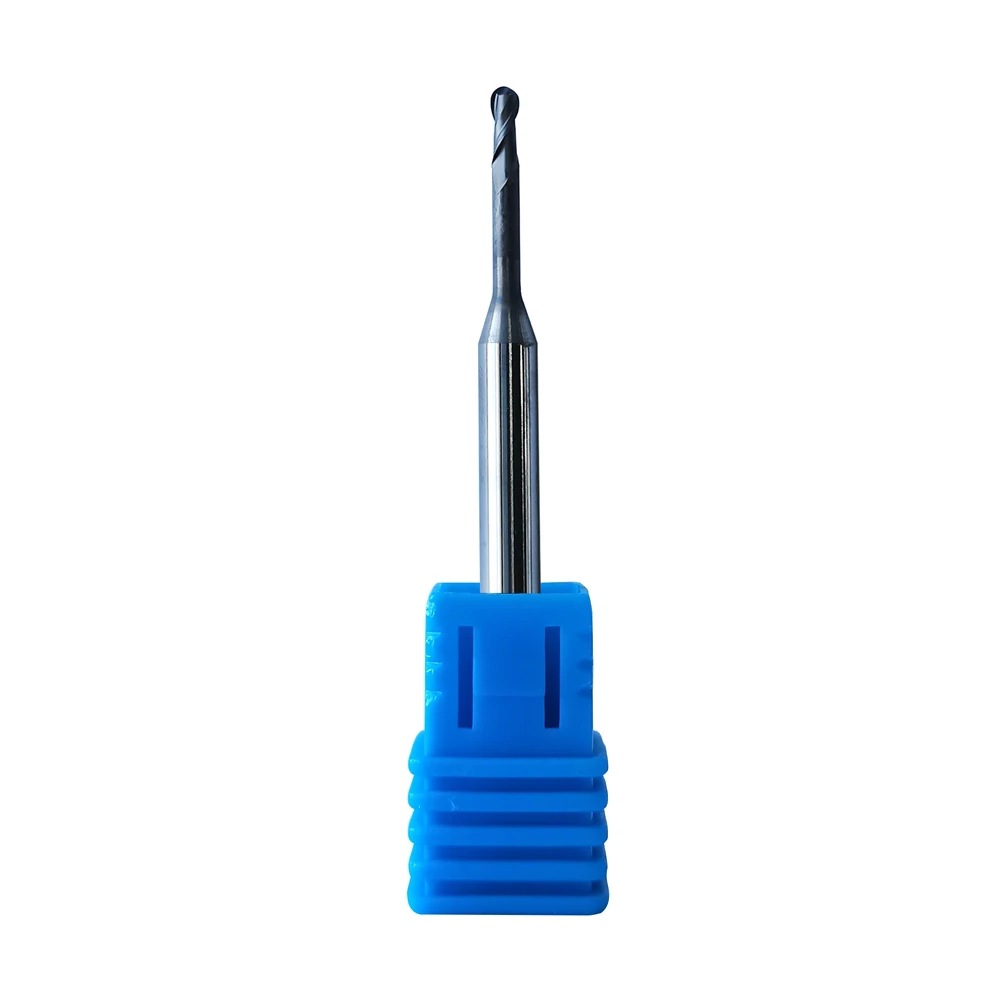
Supply Roland DLC Zirconia Burs
Product Information Origin Tianjing, China Series Dental Bur Brand MSK Cutting Edge Form 2 Blade/3 Blade Ball Diameter (Mm) 0.6, 1, 2 Material Very Fine Grained Cemented Car […]
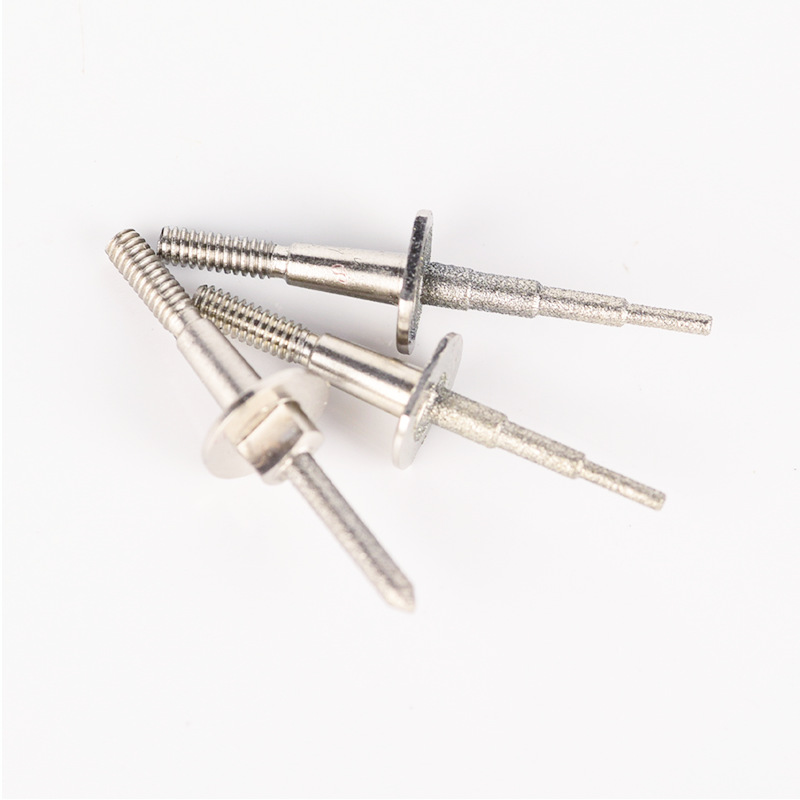
Step Bur Milling Bur Grinder for Glass Cerami
Product Information Origin Tianjing, China Shank Diameter 1.8 (mm) Brand MSK Scope Of Application CEREC3 Grinding Equipment Material Stainless Steel/Carbide Main Sales Areas […]
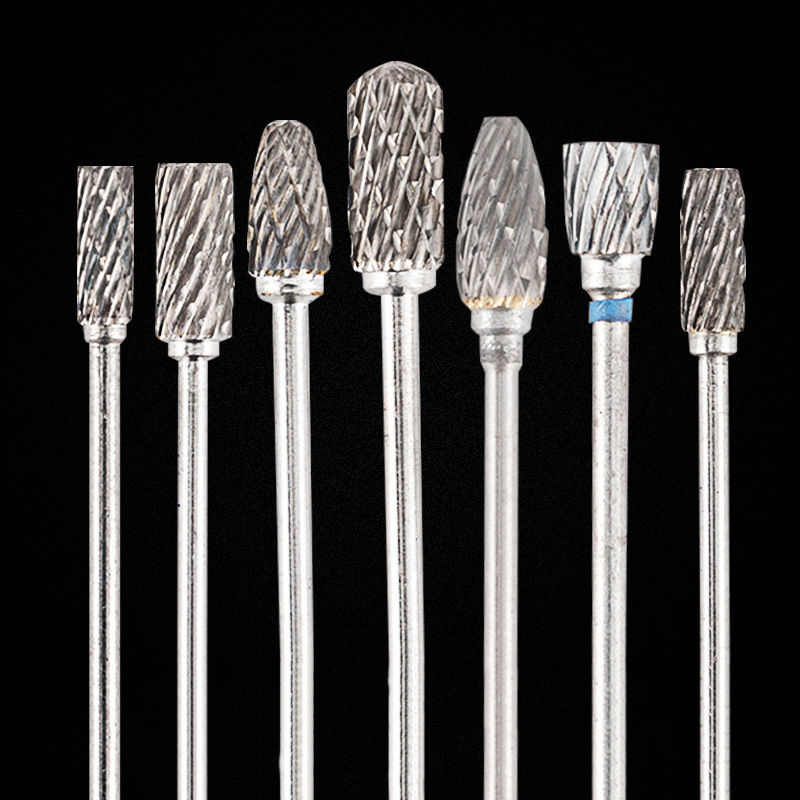
HP Deburring Carbide Burs
Product Information Brand MSK Material Tungsten Steel Model Grinding Head Custom Processing Yes Feature: The dental grinding head is made of tungsten steel with stabl […]
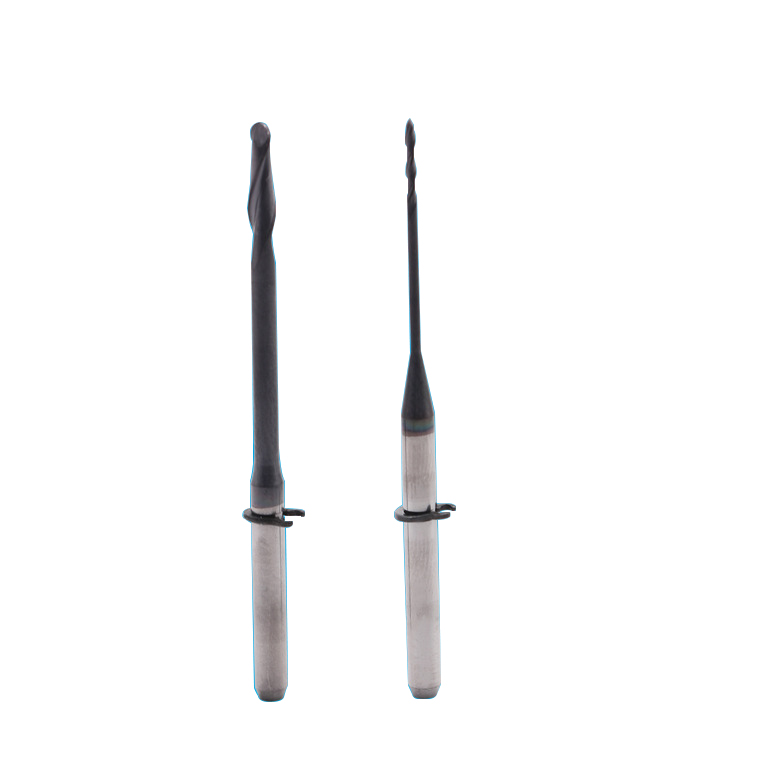
Dental CAD/CAM Milling Burs
Product Information Origin Tianjing, China Material Stainless Steel Brand MSK Applicable Machine Tools A Variety Of Options Custom Processing Yes Whether To Coat No Is It a […]
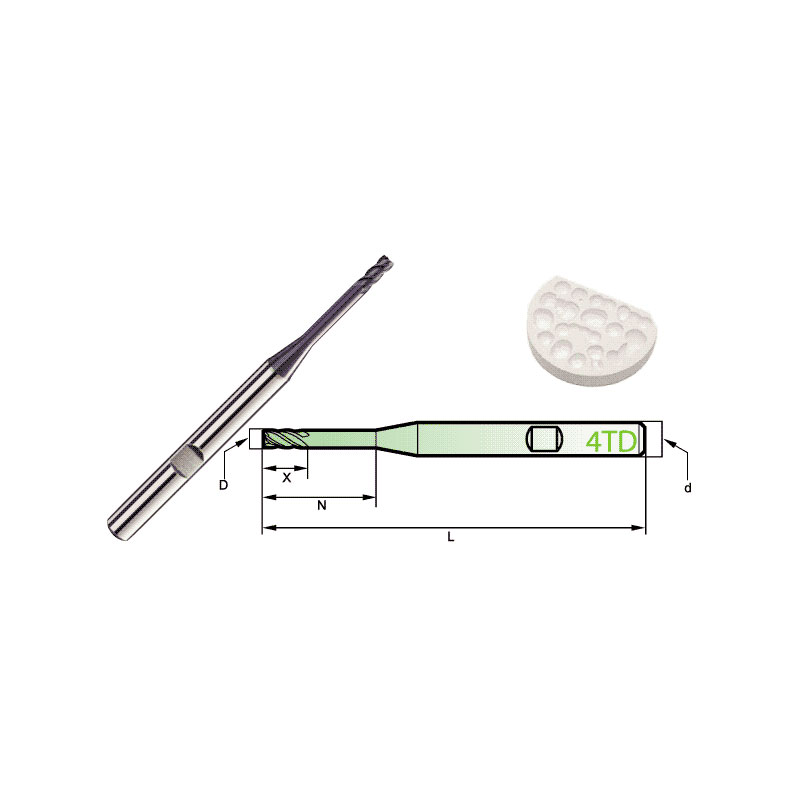
Carbide Roland CAD/CAM Burs
Product Information Origin Tianjing, China Brand MSK Number Of Blades 4 Product Name Dental Special 4-Blade End Mill Model D Number Of Blades Z X N L d 4TD2060HB 2 4 […]
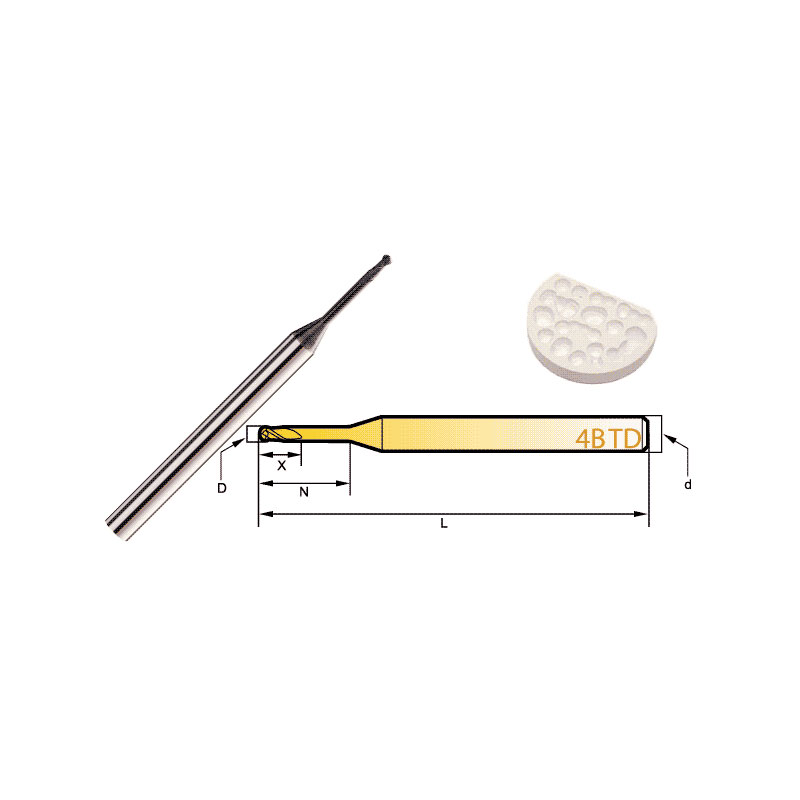
Diamond Bur Ball Round
Product Information Product Name Dental 4-Flute Ball End Mill Brand MSK Model D Number Of BladesZ X N L d 4BTD2060 2 4 6 6 50 3 4BTD2010 2 4 6 10 50 3 4BTD2016 2 4 6 […]
Post time: 2023-06-28