In order to reasonably select the process parameters and the machining path planning method during the milling of the primary sintered zirconia ceramic denture, in order to improve the machining efficiency and quality, a function aimed at improving the material removal rate and reducing the surface roughness was established, using the ideal point method, The minimum deviation method and the linear combination method are used to optimize the process parameters in the finishing stage. Taking the surface machining of the molar crown as an example, the UG CAM system is used to plan the tool machining path. The rough machining adopts cavity milling, and the finishing machining adopts fixed axis milling. There are three planning methods: surface milling reciprocating mode, regional milling following peripheral mode, and regional milling reciprocating mode. The comparison of actual machining results shows that: under the same process parameters and tool conditions, the regional milling reciprocating mode planning method can obtain the best crown surface quality .
In recent years, the production of dentures has developed to the requirements of individuality, beauty, and efficiency . Traditional porcelain teeth are mostly made by hand, which is cumbersome in craftsmanship, low in production efficiency, and has a large number of patient visits and a high rework rate. And dental CAD The application of /CAM CNC machining technology avoids the cumbersome production process of dentures, and can be processed and formed at one time, and the patient can visit a doctor in one visit . CAM technology for denture machining has been rapidly developed in the field of prosthodontics, and new materials are combined with CAM machining technology. It has received increasing attention in China . Zirconia ceramics are widely used in the oral cavity due to their excellent physical and chemical properties that can replace titanium and other alloy materials, excellent biocompatibility, and close to the natural color of natural teeth . The application in the field of repair is increasingly widespread . In CAM processing, due to the high hardness of the fully sintered zirconia ceramic material, the direct processing efficiency is low. The secondary sintering technology refers to the use of primary sintered zirconia (lower hardness). ) for processing and then secondary sintering to obtain dentures.
Studies have shown that compared with primary sintering, the performance of zirconia ceramics sintered by secondary sintering is not much different, but the machinability is greatly improved. Kato et al. found that the processing quality of zirconia ceramics sintered at 850 ℃ for the first time is the best. Good. Lei Xiaobao et al. studied the grinding and milling of primary sintered zirconia ceramics, and established the functional relationship between roughness and process parameters through experiments in milling, and optimized the process parameters with the minimum roughness as the goal. , and used JDPaint software for tool path planning. In the processing planning of dentures, Lu Peijun et al. used Surfacer 10.5 to plan and process dentures. used Powermill software to plan the tool path for denture processing. At present, in the processing of primary zirconia ceramic dental restorations, the parameters of each processing stage are different. The research on optimization selection and processing efficiency is not deep enough. As a general CAD/CAM system software at home and abroad, UG has powerful surface roughing and finishing functions, but there are few reports on its application in the processing path planning of denture restoration manufacturing.
In this paper, the reasonable selection of process parameters and tool path planning methods during the milling of primary sintered zirconia ceramic dentures are studied. Taking improving the material removal rate and reducing the surface roughness as indicators, different methods are used to optimize the process parameters in the finishing stage; Taking machining as an example, the optimized process parameters are selected, the UG CAM system is used to plan the tool paths in the rough and finishing stages, and the influence of different finishing tool path planning methods on the surface quality is verified through machining experiments to explore suitable tool path planning methods.
Related Product
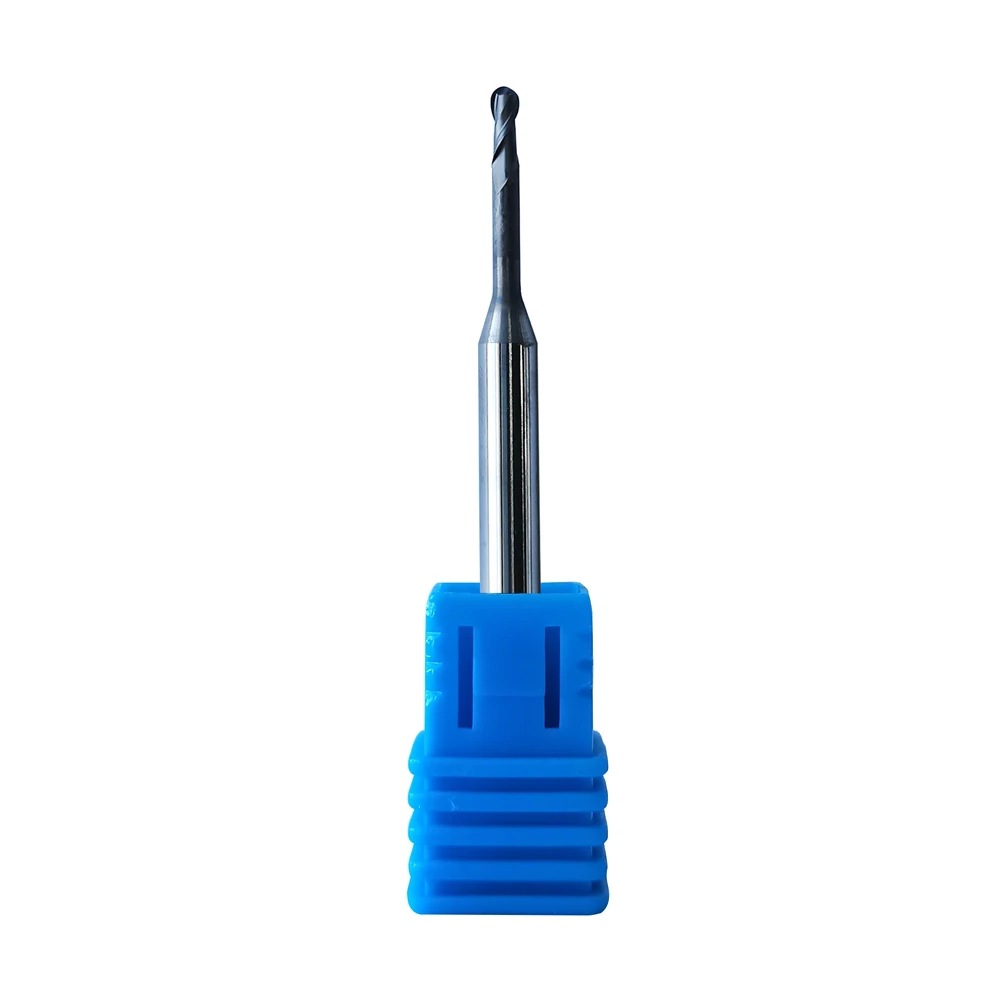
Supply Roland DLC Zirconia Burs
Product Information Origin Tianjing, China Series Dental Bur Brand MSK Cutting Edge Form 2 Blade/3 Blade Ball Diameter (Mm) 0.6, 1, 2 Material Very Fine Grained Cemented Car […]
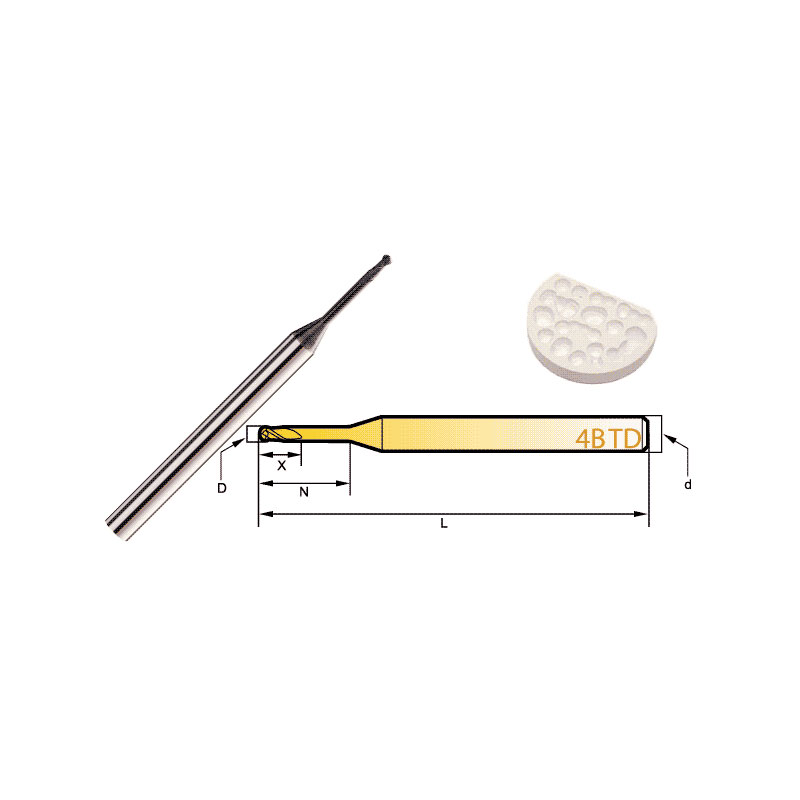
Diamond Bur Ball Round
Product Information Product Name Dental 4-Flute Ball End Mill Brand MSK Model D Number Of BladesZ X N L d 4BTD2060 2 4 6 6 50 3 4BTD2010 2 4 6 10 50 3 4BTD2016 2 4 6 […]
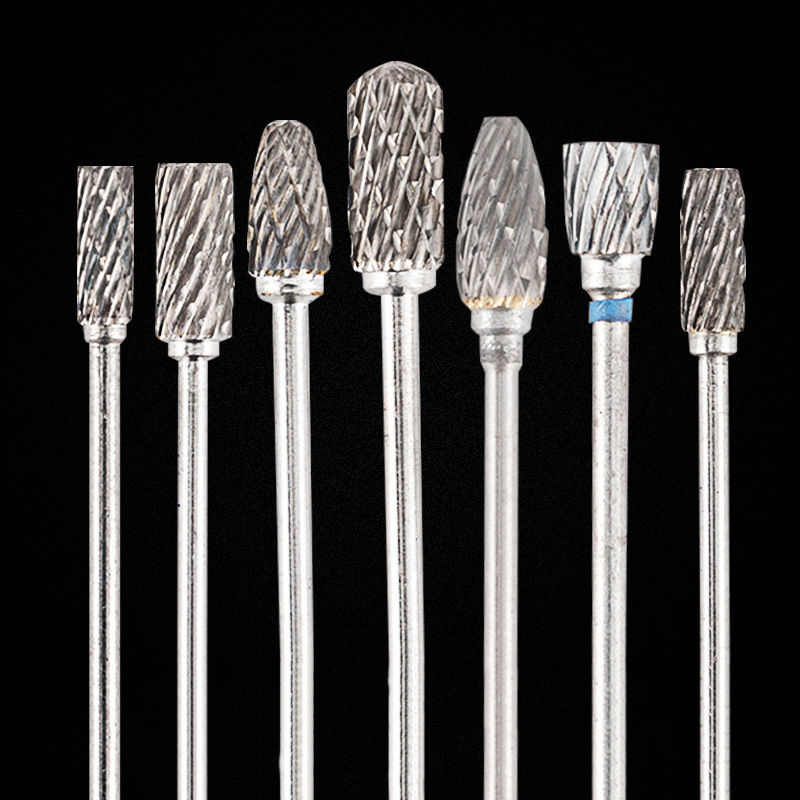
HP Deburring Carbide Burs
Product Information Brand MSK Material Tungsten Steel Model Grinding Head Custom Processing Yes Feature: The dental grinding head is made of tungsten steel with stabl […]
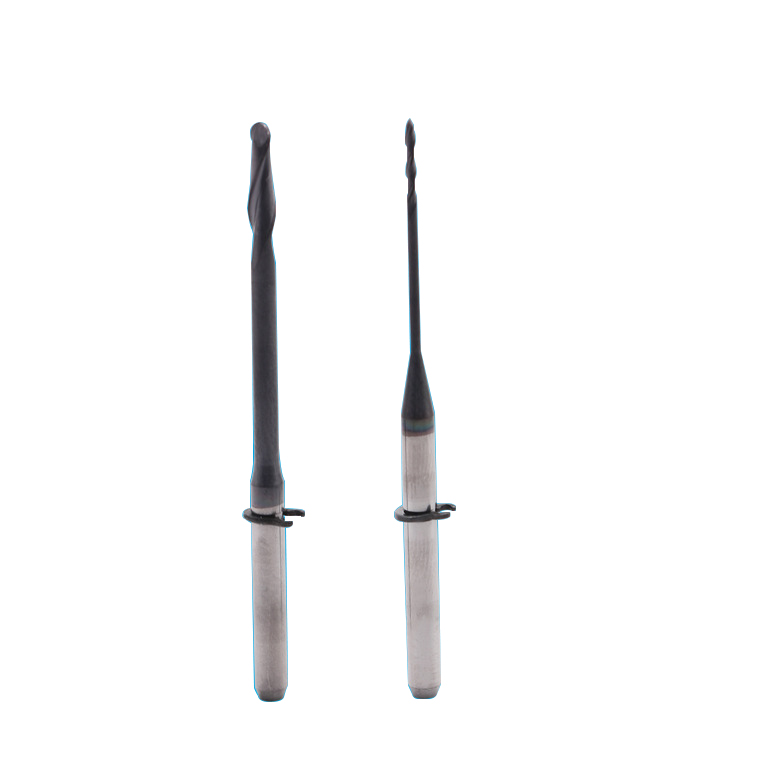
Dental CAD/CAM Milling Burs
Product Information Origin Tianjing, China Material Stainless Steel Brand MSK Applicable Machine Tools A Variety Of Options Custom Processing Yes Whether To Coat No Is It a […]
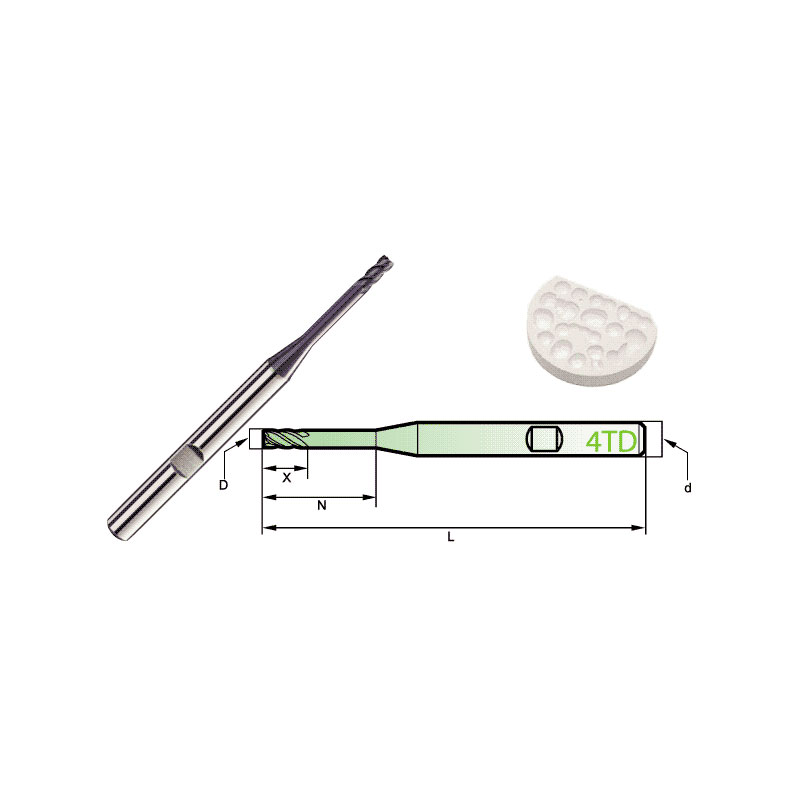
Carbide Roland CAD/CAM Burs
Product Information Origin Tianjing, China Brand MSK Number Of Blades 4 Product Name Dental Special 4-Blade End Mill Model D Number Of Blades Z X N L d 4TD2060HB 2 4 […]
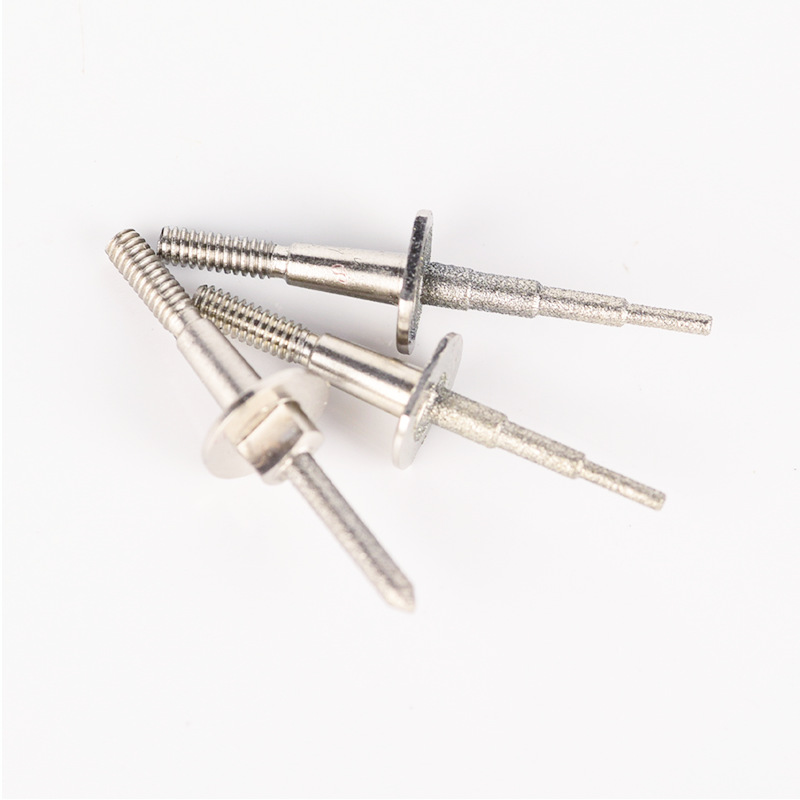
Step Bur Milling Bur Grinder for Glass Cerami
Product Information Origin Tianjing, China Shank Diameter 1.8 (mm) Brand MSK Scope Of Application CEREC3 Grinding Equipment Material Stainless Steel/Carbide Main Sales Areas […]
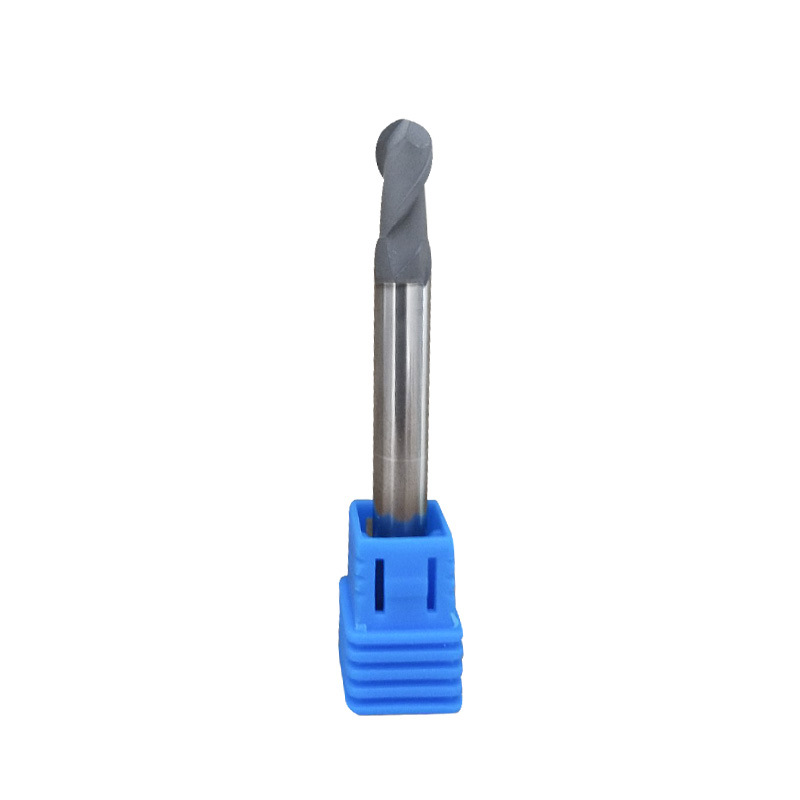
Diamond Coating Round Diamond Cutters
Product Information Origin Tianjing, China Series U Series Brand MSK Cutting Edge Form Helical Structure Ball Diameter (Mm) 3 Material Carbide Minimum Cutting Diameter At Th […]
Post time: 2022-06-08