From the workshop to the dental office, carbide burs represent a dependable and efficient way to work with tough materials. These sleek cutting tools come in numerous forms and sizes, giving their wielder a plethora of options for honing, shaping, and grinding hard items to meet their crafting needs. Such widespread utility proves that carbide burs are a staple of industrial and medical workspaces everywhere.
A wide selection of materials can be utilized in the crafting of carbide burs, such as tungsten carbide, cobalt and steel. While each has its own merits, tungsten is the prevailing choice given its sturdiness, enduringness and impenetrability. But for more challenging materials, cobalt-based burs are available to ensure successful and accurate machining.
The blade of a carbide bur is constructed from diverse sized and shaped teeth or flutes. Depending on the purpose, the number of rows of saw-like teeth can vary. Carbide burs are regularly used in power tools such as electric drills, air compressors, and dental gear.
When it comes to tackling tough materials, especially metals, carbide burs are essential. Rotary burs are the type typically used for smoothing and refining operations as they employ fast rotation to do the job. On the other hand, reciprocating burs are better for removing large amounts of material – these function at lower speeds but move back and forth for maximum effectiveness.
With their unique ability to accurately machine various materials (e.g. metals, plastics, and composites), carbide burs play a critical role in many industries such as automotive, aerospace, and medical. These burs are often utilized for tasks like drilling, reaming, counterboring, and countersinking to deliver superior performance and excellent results.
When it comes to cutting tools, carbide burs are leaps and bounds ahead of the rest. With an aptitude for highly accelerated performance, they can achieve a speed of up to 10x that of other cutting instruments. Reducing vibration and noise while offering unparalleled preciseness, carbide burs provide powerful support for tight machining works.
Although carbide burs are more robust than other cutting tools, their longevity is often diminished by their higher price tag. Not only are these burs pricier than other varieties, but their susceptibility to damage leads to shorter lifespans, necessitating more frequent replacements.
Cutting through even the toughest of materials, carbide burs come in a vast array of shapes and sizes and are impressive instruments for grinding, shaping, and machining. Whether you need to work on metal, wood, or even teeth, these multi-functional tools provide all you need with their incredible strength and precision.
For the diverse needs of machining, various materials are used in the construction of carbide burs. The most popular one is tungsten carbide, a material renowned for its resistance to wear and incomparable hardness. Although cobalt carbide burs are also available, they are generally reserved for more challenging tasks where harder materials need to be machined with precision.
A carbide bur is fitted with sharp-edged teeth or flutes. The counts, widths, and shapes of these teeth are made to fit a specific purpose. These burs may then be found in power tools such as electric drills, air tools, and dental drills, used for cutting and other applications.
A variety of operations can be completed using two standard carbide burs: rotary and reciprocating. Rotary burs spin at high revolutions, making them ideal for grinding, honing, and finishing. When higher power is needed, a reciprocating bur will be the tool of choice, as it moves back and forth at a lower velocity to effortlessly remove material.
By way of a variety of industries such as automotive, aerospace, and medical, carbide burs are essential for manufacturing products. Not only are they a useful tool for machinating metals, plastics, and composites, but they can also be employed for operations from drilling to reaming, counterboring and countersinking.
Carbide burs stand out among cutting tools for their remarkable rate and accuracy. Rather than relying on typical cutting gear that works at a much more sluggish rate, carbide burs can reach speeds up to 10 times faster, allowing users to get through jobs quickly and with minimal disruption from vibration and noise. Moreover, the tool’s high accuracy makes it ideal for precision machining.
While carbide burs boast superior cutting capabilities, their high cost and short lifespan make them a less-than-ideal choice. Not only do they burn out faster than other tools, but they are much more prone to damage, resulting in the need to replace them more regularly.
Related Product
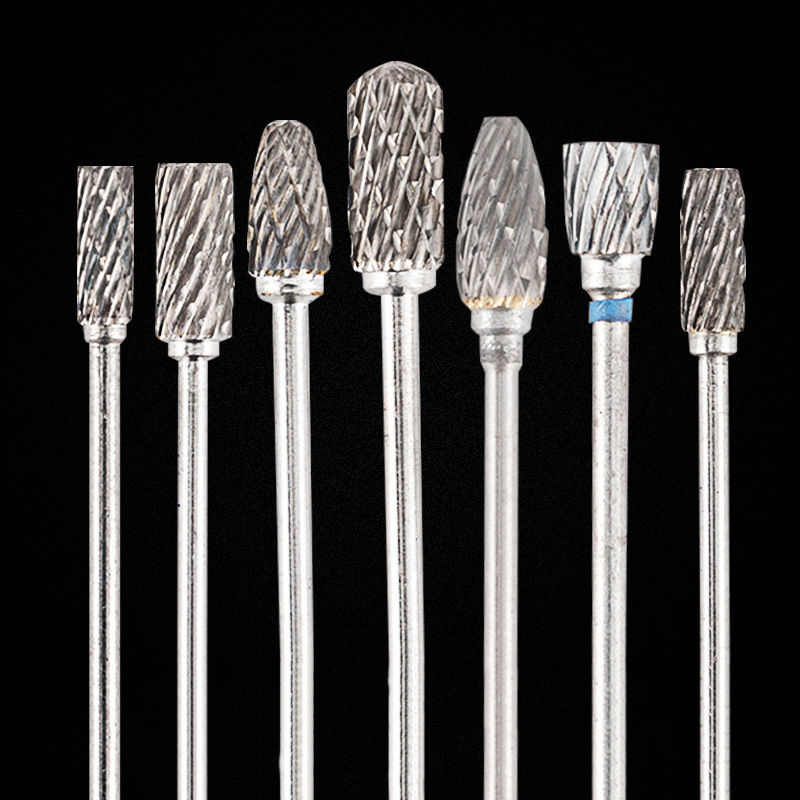
HP Deburring Carbide Burs
Product Information Brand MSK Material Tungsten Steel Model Grinding Head Custom Processing Yes Feature: The dental grinding head is made of tungsten steel with stabl […]
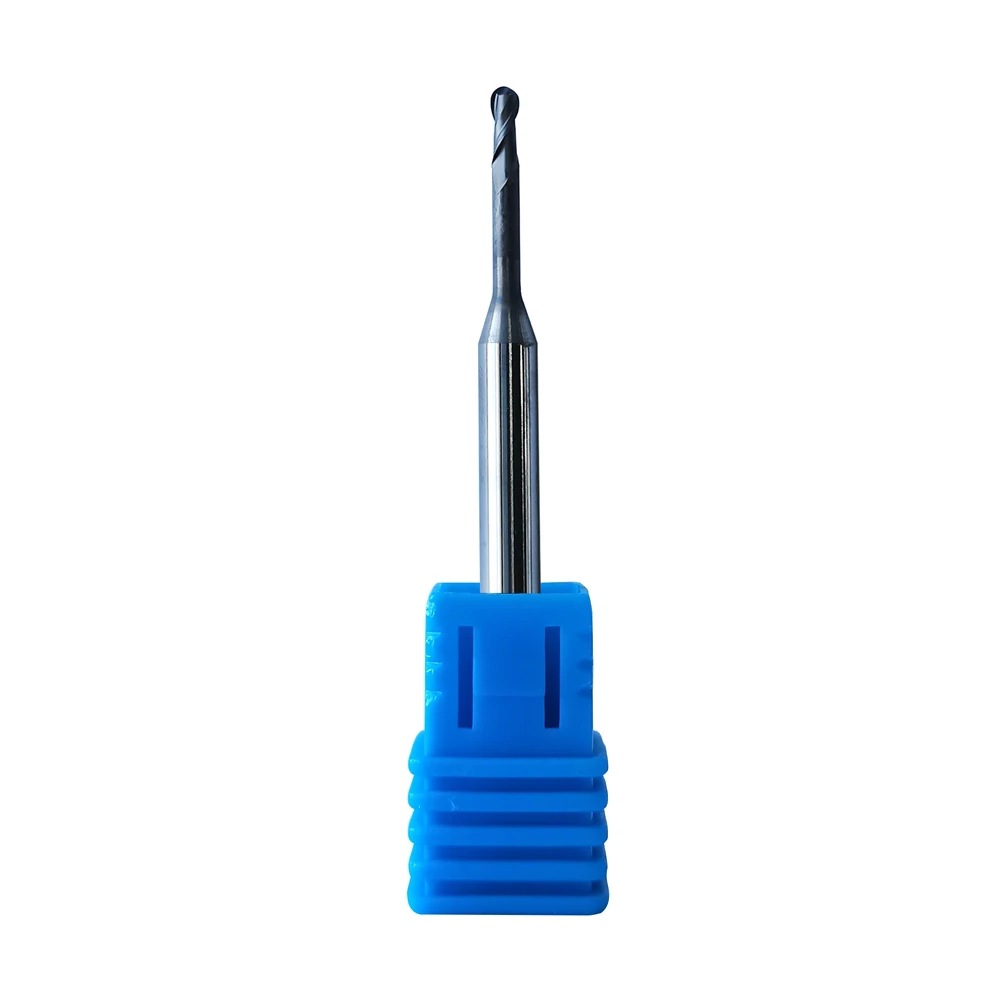
Supply Roland DLC Zirconia Burs
Product Information Origin Tianjing, China Series Dental Bur Brand MSK Cutting Edge Form 2 Blade/3 Blade Ball Diameter (Mm) 0.6, 1, 2 Material Very Fine Grained Cemented Car […]
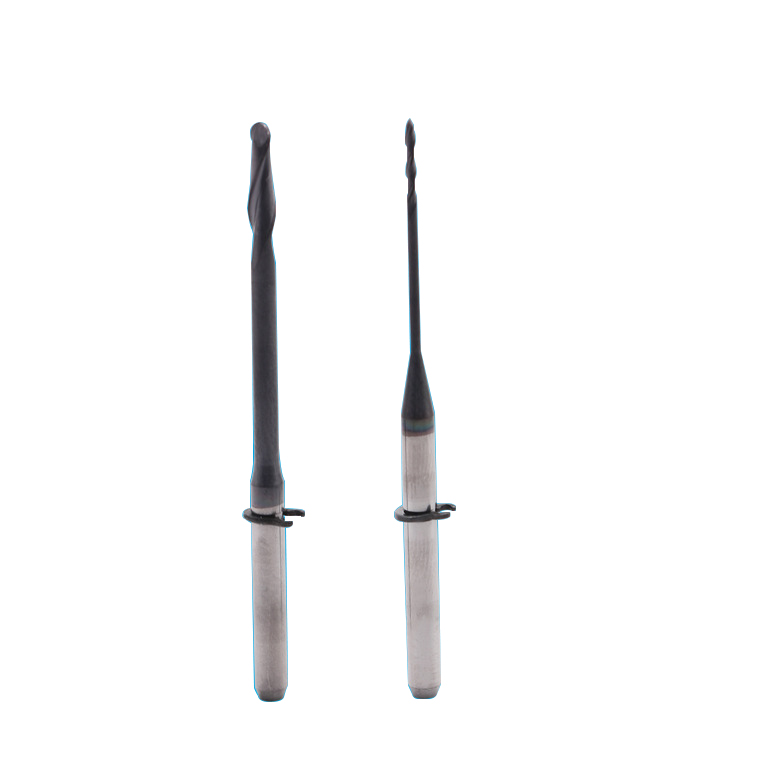
Dental CAD/CAM Milling Burs
Product Information Origin Tianjing, China Material Stainless Steel Brand MSK Applicable Machine Tools A Variety Of Options Custom Processing Yes Whether To Coat No Is It a […]
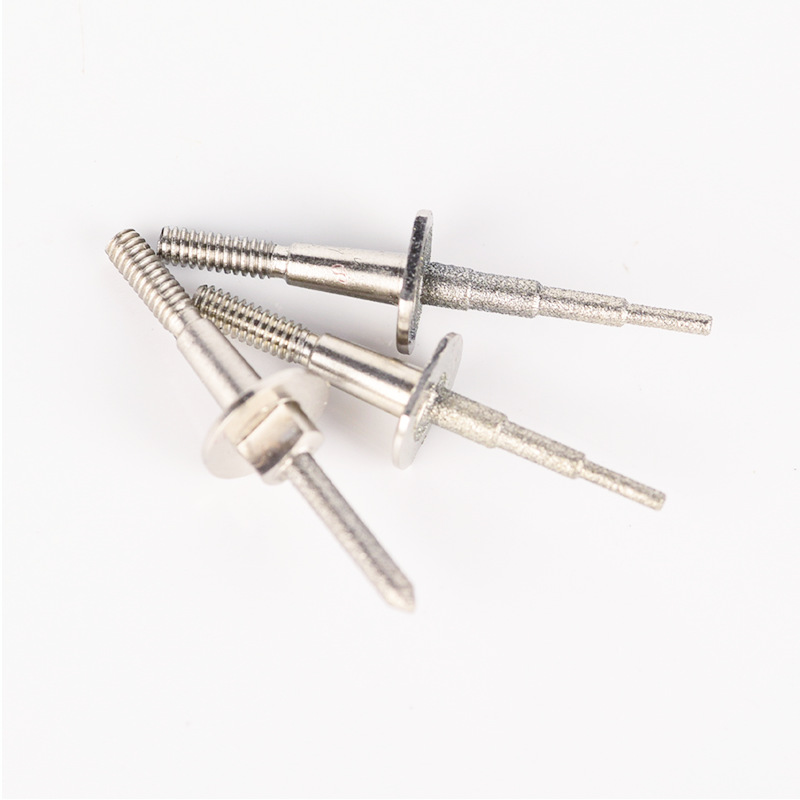
Step Bur Milling Bur Grinder for Glass Cerami
Product Information Origin Tianjing, China Shank Diameter 1.8 (mm) Brand MSK Scope Of Application CEREC3 Grinding Equipment Material Stainless Steel/Carbide Main Sales Areas […]
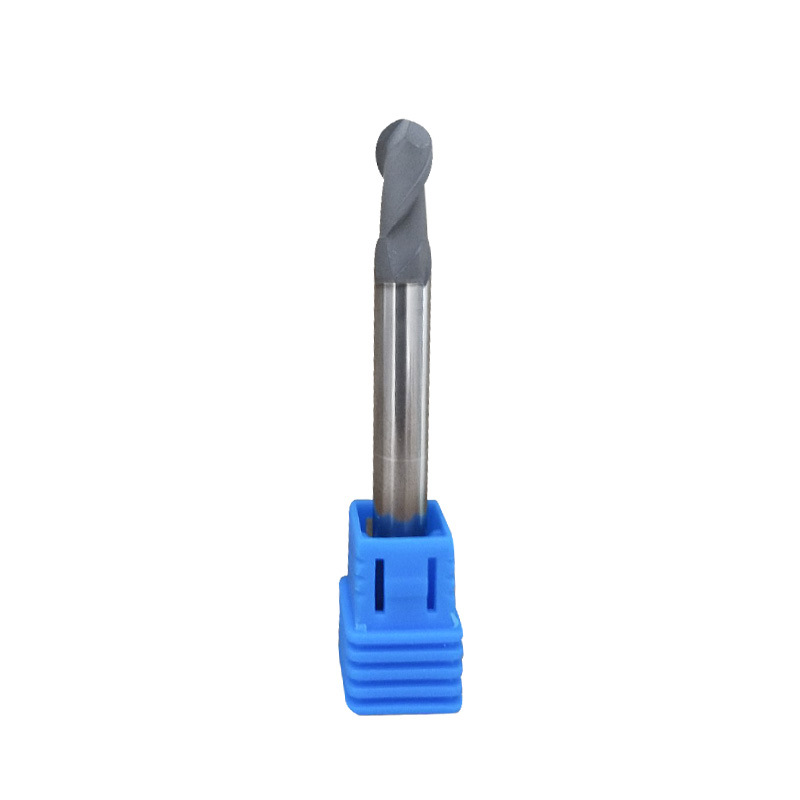
Diamond Coating Round Diamond Cutters
Product Information Origin Tianjing, China Series U Series Brand MSK Cutting Edge Form Helical Structure Ball Diameter (Mm) 3 Material Carbide Minimum Cutting Diameter At Th […]
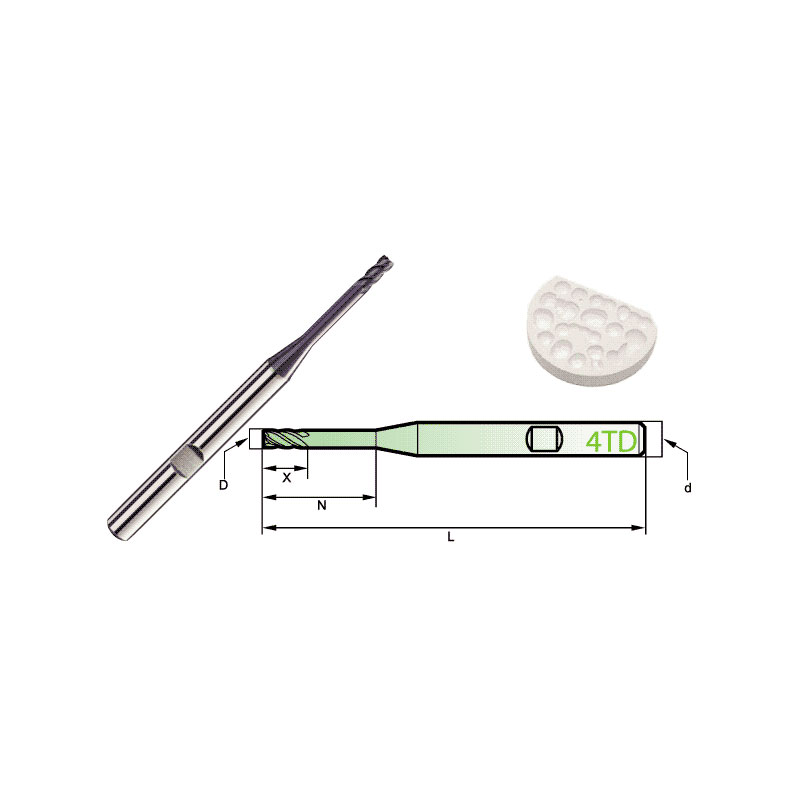
Carbide Roland CAD/CAM Burs
Product Information Origin Tianjing, China Brand MSK Number Of Blades 4 Product Name Dental Special 4-Blade End Mill Model D Number Of Blades Z X N L d 4TD2060HB 2 4 […]
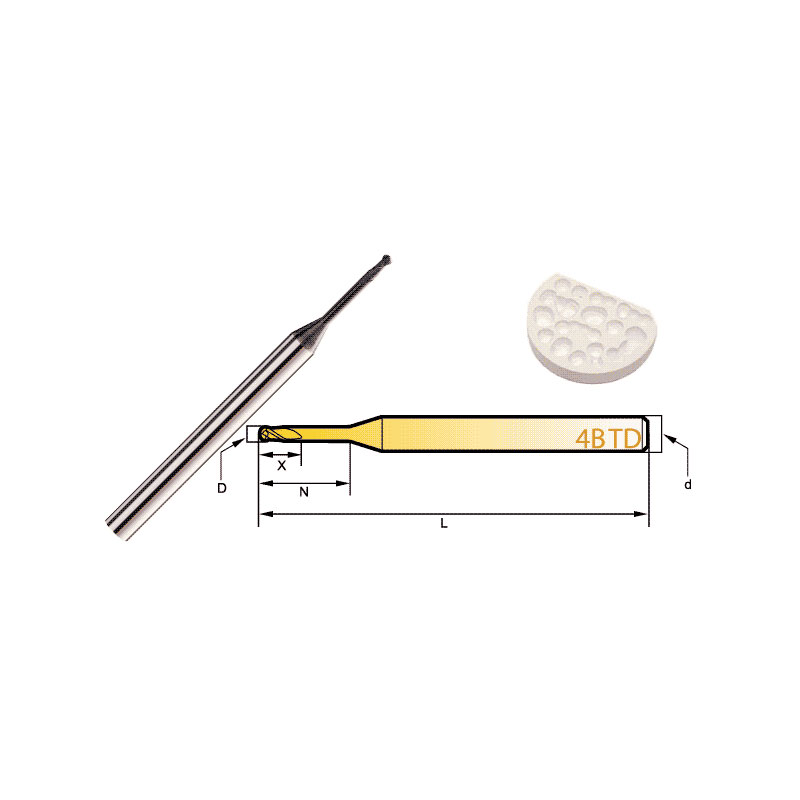
Diamond Bur Ball Round
Product Information Product Name Dental 4-Flute Ball End Mill Brand MSK Model D Number Of BladesZ X N L d 4BTD2060 2 4 6 6 50 3 4BTD2010 2 4 6 10 50 3 4BTD2016 2 4 6 […]
Post time: 2023-06-21